News and Press Releases
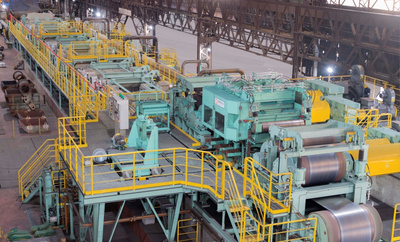
London, 06 April 2022
Primetals Technologies receives final acceptance for revamping continuous pickling line at Okayama plant of Tokyo Steel
- First ever installation of iBox pickling tank at an electric steel plant – resulting in lower energy consumption and higher pickling efficiency
- 50-ton tension leveler type scale breaker improves flatness for high-tensile steel
Primetals Technologies recently received the final acceptance certificate (FAC) for revamping the continuous pickling line for hot-rolled strip at the Okayama plant of Tokyo Steel Co., Ltd. The project included installation of a polypropylene iBox pickling tank with acid concentration control, and the addition of a 50-ton tension leveler type scale breaker. An energy-saving, high-efficiency pickling system, the iBox has been delivered to 23 integrated steel plants worldwide. The system installed at Tokyo Steel's Okayama plant achieves the same productivity at hot descaling and reduction in energy consumption with both integrated and EAF based steel plants.
The project scope involves replacing the cross-injection pickling system of the acid-resistant brick lining, in operation since 1995, with the iBox. Made of polypropylene, a superior material in heat retaining, the iBox improves pickling capacity without using an electric pump required in conventional jet pickling tanks to circulate the acid solution.
The iBox has immersion boxes inside through which strips travel guided by rolls and skids. Formed by the immersion boxes, a narrow rectangular channel generates a strong shear flow used in the pickling process for accelerating the acid-liquid reaction. In addition, the Acid Concentration Control System (ACCS) regulates acid supply in each tank by using Primetals Technologies’ proprietary algorithm to predict and calculate the descaling distribution and pickling reaction. The pickling line processes hotrolled coils ranging from 1.5 to 6.0 millimeters in thickness and from 840 to 1.340 millimeters in width.
One of Japan’s largest steel producers relying on electric steelmaking, Tokyo Steel operates four domestic production plants and has been ranked the country's top producer of H beams for the past eight consecutive years. The portfolio includes a wide range of products, such as H beams, plates, and hot-rolled coils. Focusing on the trend toward green steel, the company has set a long-term environmental vision – "Tokyo Steel EcoVision 2050". With a policy that emphasizes decarbonization and circular economy initiatives, it leads the industry in terms of environmental awareness and circular economy.
Primetals Technologies has unrelentingly been improving the pickling system ever since Mitsubishi Heavy Industries, Ltd. Hiroshima Shipyard and Machinery Works, the predecessor and now the parent company of Primetals Technologies Japan, delivered its first pickling plant to Nippon Steel Sheet Company Osaka Works (currently, Nippon Steel Corporation Setouchi Works in Osaka) in 1954. Over 100 plants have been installed worldwide.
Polypropylene iBox installed at the Okayama Plant of Tokyo Steel Co., Ltd.
Primetals Technologies, Limited, headquartered in London, United Kingdom, is a pioneer and world leader in the fields of engineering, plant building, and the provision of lifecycle services for the metals industry. The company offers a complete technology, product, and services portfolio that includes integrated electrics and automation, digitalization, and environmental solutions. This covers every step of the iron and steel production chain—from the raw materials to the finished product—and includes the latest rolling solutions for the nonferrous metals sector. Primetals Technologies is a joint venture of Mitsubishi Heavy Industries and partners, with around 7,000 employees worldwide. To learn more about Primetals Technologies, visit the company website www.primetals.com.