Metals Intelligence
Convert your data into insights and actions
The performance of a highly automated steel plant can significantly be improved by leveraging the power of existing data. Production data should be stored in a structured way in a Data Warehouse. Business Intelligence tools provide answers to production-related questions. Data-driven methods can generate insights into how to improve a steel plant's performance. Ideally, these insights are automatically converted into standardized actions. Digital assistants provide recommended actions and supervise operators.
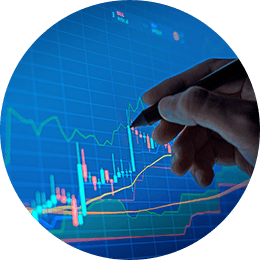
DIGITAL ASSISTANTS — GUIDANCE AND QUALIFIED SUPPORT
Primetals Technologies offers various digital assistants providing precise guidance and qualified support for operators, maintenance engineers, and metallurgists for individual production steps and all production units involved, e.g., to:
- Support the furnace operator to achieve best practice operation
- Detect quality deviation during running production and advise the operator on how to react
- Support in checking all implemented constraints and production rules
- Digitalize operational knowledge in a structured way
- Standardize production processes with rules
- Digitalize process know-how and provide it when needed
- Evaluate implemented rules by consideration of process models
- Give a voice to urgent tasks in a steel plant
Asset Life Expert (ALEX)
Primetals Technologies has developed an intelligent digital assistant called Asset Life Expert (ALEX), which ensures the highest availability of your steel plant. ALEX acts as an innovative, centralized expert system for intelligent condition monitoring, including standard vibration monitoring. ALEX enables operators and maintenance engineers to efficiently analyze data and alerts from a range of sensors at a steel plant, evaluate the generated insights, and identify the appropriate courses of action to ensure the reliable and efficient operation of the plant. ALEX guides and assists operators and maintenance engineers through daily tasks, offering clear status information and recommending intelligent actions.
DIGITAL TWINS — ACCELERATE THE CONTINUOUS PERFORMANCE IMPROVEMENT OF YOUR PLANT
Digital twins are digital representations of plants, automation systems, processes, products, or logistics which allow steel producers to analyze and experiment without the risk of production loss, damage to equipment, or safety in the real plant. The no-risk virtual simulation can replace production tests, reduce product development costs, and accelerate staff education via virtual trainings.
Primetals Technologies offers different digital twins for different applications in a steel plant, such as:
- The plant digital twin is a 3D model including piping and infrastructure that allows plant design, reduction of risks and damages, and eliminates risks of collisions
- The automation digital twin is applied to simulation and optimization for the plant automation and is additionally used for training
- The process digital twin holds data, and a model of the metallurgical process can be used to simulate and optimize processes and is used for operator training
- The product digital twin supports product development, increases development speed, and is used to optimize quality and production both for metallurgical processes and the geometry of the final products
- The logistics digital twin analyzes and optimizes intralogistics processes and supports optimizing layouts and material flows
- A holistic digital twin allows the full digital representation of a plant, including processes, products & operations, and the entire metallurgical process
DATA ANALYTICS — CONVERT BIG DATA INTO VALUABLE INSIGHTS
The use of data analytics is on the verge of becoming an essential factor in metals production. Data analytics will facilitate the next step in overall performance optimization, making the – production process smarter, more adaptive, and more efficient. This increase in machine-applied intelligence will lead to even greater levels of consistency in terms of product quality, help speed up product development—especially for higher-quality steels—, support operators to discover the root cause of any production problems they may be facing, enable smaller production runs with a minimal loss in productivity, and also make it easier to adjust a plant’s production process when the raw-material mix changes or if the product mix is extended. Additional areas of application will come to the fore as the technology matures.
Examples of analytic case studies
METALS BUSINESS INTELLIGENCE — DATA-DRIVEN DECISION SUPPORT
Metals Business Intelligence from Primetals Technologies is a data-driven decision assistance solution that supports plant and production managers and process engineers in analyzing and visualizing production and quality data. Data-driven decision support results in faster and better business decisions.
Today a business intelligence solution has to deliver insightful and actionable information without requiring a data scientist to collect, prepare and analyze complex data and process it into reports, which are suitable as a basis for intelligent management decisions. Additionally, it is essential to define relevant KPIs to measure processes and performance.
Metals Business Intelligence from Primetals Technologies offers a comprehensive set of tools for extensive production data analysis packed into a powerful, flexible, and easy-to-use web-based front end.
Key Features
- Metals Data Warehouse including a long-term data archive and data mart for business intelligence
- Unified business intelligence across all user groups
- Ad-hoc report designer with interactive functions such as filtering, charting, and custom calculations
- Dashboards with a collection of interactive reports, charts, KPIs, and controls
- Self-service business intelligence with a virtual view of data sources that simplifies information visualization with data-level-security
- Easy integrability of the Intelligence Data Mart with other business intelligence tools
CENTRAL OPERATION COCKPIT (COC) — INCREASED FOCUS FOR OPERATORS
The demand for increased productivity, stable production processes, and improved product quality require the reduction of manual intervention in the production process. Therefore, the level of plant operation autonomy has to be increased on the one hand. But on the other hand, a steel producer wants to avoid enlarging his operator team to monitor the increased number of automation systems.
Primetals Technologies has developed the Central Operation Cockpit (COC) to overcome this challenge. The Central Operation Cockpit is an innovative core technology enabling new operation concepts providing the basis for an entire production unit's remote and centralized operation and one essential enabler for an autonomous or dark plant.
Benefits
- Increased focus of operators
- No information overflow – only required information is displayed to the operator
- Operators can handle entire production units in normal production condition