TANDEM COLD MILL
Efficiency and quality production of advanced steel grades.
The Tandem Cold Mill consists of three to six mill stands arranged in series to progressively and effectively reduce the thickness of the strip in a single pass. With its powerful reduction and highest production rates, the Tandem Cold Mill helps steel producers to meet the growing demand for advanced steel grades by enabling high-capacity production. The advanced features of Primetals Technologies’ Tandem Cold Mill with UC-MILL principle help to improve yield and achieve uncompromising quality of strip to meet strict tolerance requirements, while keeping operation simple and user-friendly.
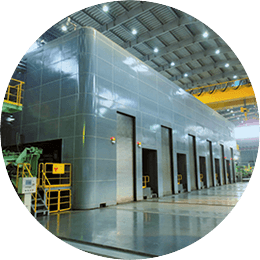
MAXIMUM APPLICATION OF UC-MILL PRINCIPLE AND ADVANTAGES
Benefits:
- Highest production rates (over 1.2 million t/a)
- Reduced roll consumption
- Flexible production
- Tight tolerances for strip thickness, shape, and high surface quality
- Low costs for operation, maintenance, and minimum down times
- Reduction in off-gauge material
- Elimination of strip threading problems
For automotive steels, high-tensile materials at thinner gauges are in growing demand as producers strive to reduce vehicle weight and consequently improve fuel consumption. As a result, there is increasing pressure to improve the performance of rolling mills. To satisfy this demand, a 5-stand Tandem Cold Mill using 6-high Universal Crown Control Mill (UC-MILL) for all stands has become the standard as a highly effective solution.
UC-Mill features:
- Work roll bending
- Work roll shifting
- Intermediate roll bending
- Intermediate roll shifting
- Super heavy reduction
- High strip shape control ability
- Cylindrical rolls for easy maintenance and operation
The standout feature of exit equipment:
A carrousel tension reel with two mandrels enables the strip to be cropped on completion of a coil, allowing the second mandrel to accept the oncoming strip without stopping the mill.
HYPER UC-Mill featuring even smaller work roll diameter can also be applied in the Tandem Cold Mill in order to meet growing market demand for thinner and harder products.
Want to know more? Go to Lifecycle Services & Integrated Plants & Solutions
COMPLETE AUTOMATION AND PROCESS CONTROL FOR TANDEM COLD MILLS
Plant productivity and product quality are substantially depending on the quality of plant automation, process control, and available process optimization functions. To get the best performance out of a plant, Primetals Technologies provides add-on specific optimization solutions for further improvement of production efficiency and strip quality, besides standardized high performance automation system.
Throughput maximization with:
- Off Gauge Optimizer for integrated rolling process
- Speed Optimization System for throughput optimization
Excellent strip quality with:
- Roll Eccentricity Expert for uniform and accurate strip thickness
- Coil Eccentricity Expert for uniform and accurate strip thickness
- Flatness Expert - Model based Automatic Flatness control
- ChatterMon / Mill Chatter Monitoring with automatic process speed adaptation
Production flexibility and special steel grades:
- Precise mill setup by high-sophisticated rolling models complying with changing production requirements and high strength steel qualities
- Neural network based adaptation and setups promising high product flexibility and easy extension of the production to new materials
- Optimized weld seam rolling supporting flexible production and obtaining minimum off-gauge
TECHNOLOGY AND MODERNIZATION PACKAGES
Get striking results with incremental investments
Name | Short Description |
---|
Name | Short Description |
---|
Name | Short Description |
---|
Name | Short Description |
---|
Name | Short Description |
---|
Name | Short Description |
---|
Reference Story: TCM for Thin Gauge and High Speed Rolling
Customer:
Posco-Vietnam, Phu My, Vietnam
Type of plant:
Coupled picking line and tandem cold mill (PL-TCM)
Technical Data:
Product: Low Carbon Steel, High Strength Steel
Strip Thickness: Entry 1.8 to 5.0 mm, Delivery 0.15 to 1.6 mm (for construction)
Strip Width: 700 to 1,570 mm
Rolling Speed: Max. 1,700 m/min
Mill Type: 6-high UC-Mill (No.1 to 5 Stand)
Our solution:
The 5 feet 5-stand UC-MILL which features high reduction by small work roll and high shape controllability achieved high speed rolling of very thin products. This marked the first PL-TCM in Vietnam and has been in stable operation since its expeditious start-up.