News and Press Releases
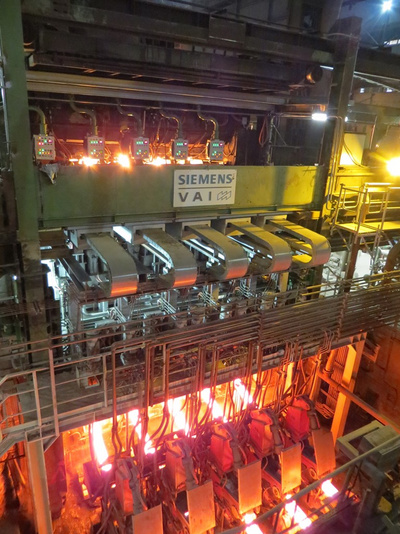
London, 16 September 2015
Primetals Technologies receives final acceptance from Elbe-Stahlwerke Feralpi for continuous billet caster
- Technical improvements to the machine head and secondary cooling improve quality
- Production capacity increased by 20 percent to 1.2 million metric tons per annum
- Modular design and pre-assembly shorten installation and downtimes
Elbe-Stahlwerke Feralpi GmbH (ESF), a German steel producer and part of the Feralpi Group, has issued the final acceptance certificate for a modernized, five-strand continuous billet caster in its Riesa plant. Primetals Technologies received the order in May 2014. The aims of the project were to improve the internal and surface qualities of the billets, and to increase the production capacity by 20 percent. This was achieved by installing a new machine head, which included DiaMold molds and a retractable DynaFlex oscillator, as well as by optimizing the secondary cooling. The new plant has a modular design, and was pre-assembled to keep installation and downtimes short.
The five-strand continuous billet caster owned by ESF in Riesa was installed in 1994 by a third-party supplier. It had an annual production capacity of around one million metric tons of billets with square cross-sections of 130x130, 140x140 and 160x160 millimeters. The plant has a machine radius of six meters and reaches casting speeds of up to 3.8 meters per minute. It casts low and medium-carbon steels, which are further processed in a wire rod mill in the Riesa plant. Retractable DynaFlex mold oscillators were installed to increase capacity. This solution enables the mold on a strand to be exchanged without interrupting the casting process, increasing both the productivity and the flexibility of the casting plant. All mechanical connections are released hydraulically at the touch of a button. The complete machine head, including mold and oscillator, is moved from the casting position to the maintenance position on a mobile platform. The time between stopping and restarting the strand to change a mold is between just 15 and 20 minutes. In this time, the mold is exchanged, the dummy bar is brought in, and the mold is prepared for casting. The existing secondary cooling was converted and extended by adding a fourth zone to ensure optimal cooling even at higher capacities.
To increase product quality, the casting plant was equipped with new DiaMold molds to increase product quality. The technical features of the oscillators include stroke adjust capability during operation, and the option of selecting from a range of sinusoidal and non-sinusoidal oscillation parameters. An OsciMon system monitors the movements of the molds, and visualizes the measured values of frequency and stroke in all three dimensions. The equipment installed during the course of the modernization was designed to keep downtimes as short as possible. The modular design concept was selected for its focus on ease of installation. Primetals Technologies system parts were also pre-assembled and tested according to the proven "Connect & Cast" plant conversion philosophy to shorten installation times on site. As agreed, the plant was converted during the 2014 Christmas stoppage. One major reason for winning this order was the good results Feralpi had obtained with the modernized, four-strand continuous billet caster in Acciaierie di Calvisano, Italy, which Primetals Technologies had also modernized at the beginning of 2013.
Connect & Cast is a registered trademark of Primetals Technologies in some countries
Five-strand continuous billet caster from Primetals Technologies in the Elbe-Stahlwerke Feralpi GmbH (ESF) plant in Riesa, Germany.
Primetals Technologies, Limited, headquartered in London, United Kingdom, is a pioneer and world leader in the fields of engineering, plant building, and the provision of lifecycle services for the metals industry. The company offers a complete technology, product, and services portfolio that includes integrated electrics and automation, digitalization, and environmental solutions. This covers every step of the iron and steel production chain—from the raw materials to the finished product—and includes the latest rolling solutions for the nonferrous metals sector. Primetals Technologies is a joint venture of Mitsubishi Heavy Industries and partners, with around 7,000 employees worldwide. To learn more about Primetals Technologies, visit the company website www.primetals.com.