BY-PRODUCT RECYCLING — CUTTING-EDGE TECHNOLOGIES FOR HIGHLY EFFICIENT BY-PRODUCT RECYCLING
Closed-loop recycling technologies and services from Primetals Technologies ensures efficient by-product management. The objective is always twofold: to save resources and to create value.
Around the world, government regulations concerning environmental care are becoming more stringent, also in regard to regulations for depositing and storing dust and sludge generated in the iron and steelmaking process. These by-products such as iron-containing dust, sludge, oxide fines and scales as well as, for example, lime dusts become a valuable resource and recycling becomes a profitable activity within a plant.
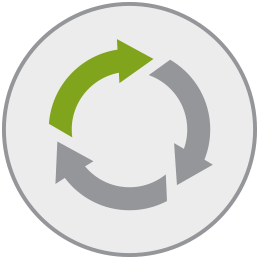
Recycling of ironmaking by-products
Ferrous briquetting – Recycling of by-products
Our solution for recycling of the by-products uses a cold briquetting process, with proven equipment and application of a suitable binder selected for each application, to ensure highest possible product quality of briquettes that can be charged into a DRI plant, blast furnace, Corex or LD (BOF) converter.
Dry slag granulation with heat recovery
Primetals Technologies, voestalpine Stahl, the FEhS – Building Materials Institute and the University of Leoben joined forces in an R&D program to develop a new dry-granulation technology using air to cool molten slag and recover the lost heat energy. The slag granulate fulfills the same criteria as wet-granulated slag for use in the cement industry.
GasFerm – Generation of added value for offgases
GasFerm is a new development in offgas recycling that simultaneously addresses the need to reduce the steel industry’s carbon footprint while improving a steelmaker’s economic competitiveness through promotion of the circular economy. This technology is developed by LanzaTech. Primetals Technologies is partner for plant implementation for the iron and steel industry.
By-Product Leaching – Special residue treatment for dry dedusting systems
Primetals Technologies MEROS technology drastically reduces the amount of hazardous off-gas components (e.g. dust, dioxine, SO2) emitted by sinter and pelletizing plants. Still the remaining by-product dust causes high costs for disposal at a hazardous landfill site. By adding a By-Product Leaching system to the dry gas cleaning plant, up to 90% of this residue dust can be reduced through special treatment steps. Thanks to its modular system it can be easily adapted to match customer requirements or environmental regulations.
Click here to learn more about our gas-cleaning portfolio for ironmaking facilities.
Recycling the by-products of steelmaking
GasFerm – Generation of added value for offgases
GasFerm is a new development in offgas recycling that simultaneously addresses the need to reduce the steel industry’s carbon footprint while improving a steelmaker’s economic competitiveness through promotion of the circular economy. This technology is developed by LanzaTech. Primetals Technologies is partner for plant implementation for the iron and steel industry.
BSSF Technology for slag processing
Slag from steel production in LD (BOF) converters and electric arc furnaces can, for example, be used as material in road or railway track bed construction. In the Baosteel Slag Short Flow (BSSF) granulation process developed by Baosteel, the liquid slag is transferred to a granulation drum where it is treated with injected water with a dwell time between three and five minutes, which significantly reduces the amount of unreacted free lime. The hermetically sealed vessel and central vapor extraction system ensure that all emissions of dust and hazardous substances are avoided. The batch-wise operating BSSF plants have short process times and a compact design.
Click here to learn more about our gas-cleaning portfolio for steelmaking facilities
Reference Story: By-product recycling
Customer
voestalpine, Texas, U.S.A.
Typ of plant
Recycling plant of ferrous materials
Our solution
Primetals Technologies and voestalpine Texas LLC. signed a contract for the basic design & engineering of a Fines Recycling Plant to be installed at the voestalpine HBI plant in Corpus Christi, Texas, USA. The pellet fines, dusts and sludge generated in the Midrex process and briquetted in the plant and are charged directly to the HBI plant as pellet substitute.