BLAST FURNACE TECHNOLOGIES – INNOVATION AND INCREMENTAL DECARBONISATION
Meeting the twin demands of extending blast furnace life and reducing CO2 emissions
Primetals Technologies has provided blast furnace engineering, project excellence and expertise world-wide for over a century. Our technologies cover the entire blast furnace process route from raw materials to clean gas and hot metal / slag processing. Our capabilities include feasibility and process studies, a wide range of technical products and solutions, environmental, CO2 and energy saving answers, automation systems, and the ability to execute the full range of project models. This capability forms the basis for successful project completion and start-up, for the complete range of solutions from small to ultra-large blast furnaces.
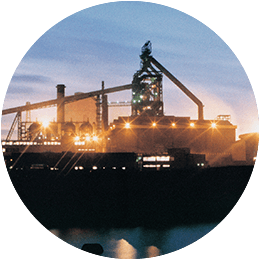
BLAST FURNACE TECHNOLOGIES FOR IMPROVED OPERATION, REDUCED OPEX AND LOWER CO2 EMISSIONS
With a global installed reference base we have the background and expertise to design, supply, build and install greenfield blast furnace operations.
We additionally offer unparalleled experience and unique capability to rebuild or extend campaigns of existing blast furnaces within a minimum outage period. Our experience has been developed and fine tuned over the years to provide project safety and certainty. By refreshing and upgrading existing equipment blast furnace operators can realize cost optimized, effective solutions.
As the environmental impact of iron and steelmaking has become increasingly important, we are focused on technologies which reduce blast furnace CO2 emissions. Approximately 95% of the CO2 emissions from blast furnace ironmaking come from the carbon fuels used., These can be mitigated by:
- Increasing performance leading to a reduced carbon requirement of the blast furnace
- Using carbon avoidance (e.g. hydrogen or hydrogen-rich gas injection into the blast furnace)
- Utilizing Carbon Capture and Utilization (CCU) technologies
Technologies that reduce CO2 emissions
Sequence Impulse Process
The latest in blast furnace technology reduces CO2 emissions, improves productivity, and provides significant operating cost savings. The process, in conjunction with existing pulverized coal injection, repurposes oxygen directly into the tuyeres by sending high energy, supersonic pulses deep into the raceway. Char materials which accumulate and block the ’dead-man’ are cleaned as a result. This leads to improved gas distribution and utilization as well as better drainage. Overall, lower fuel rate is achieved alongside an increased PCI rate and lower CO2 emissions.
Hydrogen-Rich Gas Injection
The replacement of part of the traditional carbonaceous fuels with hydrogen-bearing alternatives is a practical way to provide incremental reductions in CO2 emissions. Primetals Technologies can provide systems for the injection of natural gas, coke oven gas, and synthetic gases, and were instrumental in the design and safe implementation of the hydrogen injection system at Tata Steel, Jamshedpur in 2023
Carbon Capture & Utilization
Primetals Technologies are also providing the trial carbon capture facility which will be installed on a plant in Europe, to test the capabilities of the KM CDR ProcessTM to remove CO2 from blast furnace gases. This year-long trial will analyze the effectiveness of the Mitsubishi Heavy Industries’ world-leading amine scrubbing solution for use with blast furnace gases and will be followed by further trials with other gases. The technology has the potential to reduce steel CO2 emissions by more than 80%.
Furnace Cooling
Our references include both plate-cooled and stave-cooled solutions.
Our stave-cooled solution utilizes copper and cast iron staves reducing the requirement for a large quantity of refractory to be utilized in the furnace stack. Unique anti-bend and anti-wear innovations ensure operators enjoy a problem free, long life, furnace cooling solution.
Hot blast systems
Our technology portfolio covers Internal and External Combustion Chamber Stoves as well as Top-Fired Burner variants. Customers have benefited from our experience of over 200 hot blast system installations over the last 20 years providing the optimized hot blast conditions, whilst minimising the overall fuel consumption. Our capability ranges from small assessment studies and repairs (including hot work) through to the supply of stoves on a full turnkey basis. Energy saving tuyere stocks ensure safe, efficient supply of hot blast to the furnace.
Technologies that improve efficiency
Gas Cleaning
Our complete portfolio offers both wet and dry (Merim) gas cleaning solutions, providing optimized gas cleaning with the potential to maximize energy recovery at the TRT. Our cyclone solution offers variable efficiency to aid management of dry dusts within your plant.
Furnace Equipment
Our portfolio includes a full range of ancilliary blast furnace operational equipment:
Casthouse equipment (Taphole Mudgun, Taphole Opener, Tilting Runner, Jack Dam Drill) | Tuyere stocks wind distribution system | Bleeder valves - safety relief valve for hot and dusty environments | Equalizing and relief valves | Above burden probe - temperature and gas monitoring | Sub-burden probe | Stockline recorder | Radar level detection | Ignition lance
Want to know more? Go to Lifecycle Services & Integrated Plants & Solutions
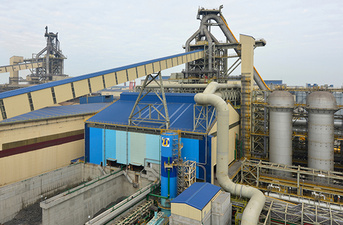
Dragon Steel No.1 and No.2 Blast Furnaces
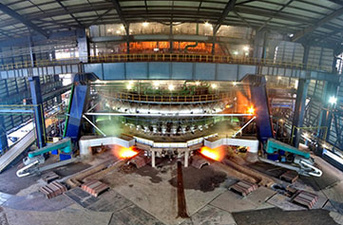
JSW No.4 Blast Furnace Casthouse
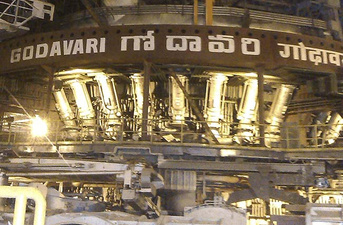
Vizag No.1 Blast Furnace Tuyere Platform
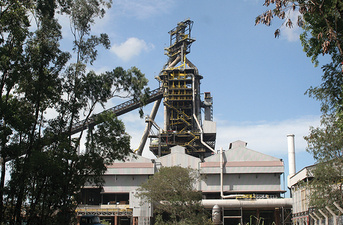
CST No.3 Blast Furnace
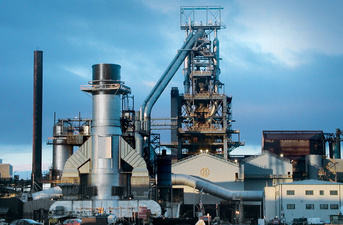
Port Talbot No.5 Blast Furnace
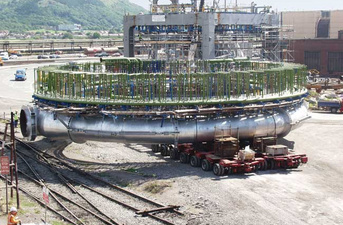
Tata Steel Ltd, Port Talbot No.5 Blast Furnace Bustle Main Transportation
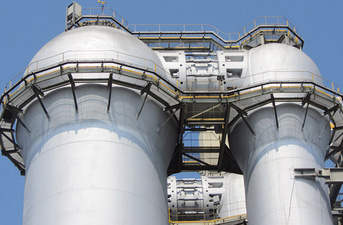
Dragon Steel No.2 Blast Furnace Stove Cross Over
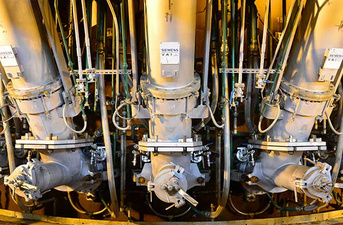
Dragon Steel No.2 Blast Furnace Tuyere Stocks
INTELLIGENT AUTOMATION FOR IRONMAKING
The blast furnace process control system in combination with the blast furnace optimization system creates the next level in intelligent blast furnace automation. The optimal interaction between sophisticated models and the expert system provides extended assistance to plant operators and minimizes the risk of human errors.
Our solutions
Cost-optimized operation, process improvements that don’t compromise burden-material selection, the highest product quality, and achieving and maintaining your desired productivity are the core challenges for our most advanced blast furnace automation system. The optimized burden calculation with precise chemical targets and subsequent closed-loop controls form the basis for producing hot metal and slag at the highest quality, while simultaneously reducing energy consumption.
The optimization system provides easy access to all process parameters, material properties, and productivity data – including charging information, chemical and physical burden material, and process measurements so that the optimal conditions for producing hot metal and slag at the best quality level can be determined. The system guarantees shift-independent plant operation where manual interactions are reduced to a minimum. The result is smooth blast furnace operation 24/7, increased equipment lifetime, and reduced production costs.
Advantages
- High productivity: blast furnace is running at peak performance while minimizing consumption of electrical energy and fuel
- Product quality: chemical properties of hot metal and slag are maintained at the desired levels
- Reduced fuel consumption: the hot metal’s temperature remains constant through small modifications of the fuel rate, based on the thermal conditions of the blast furnace
- Stable and shift-independent operation: best-practice blast furnace operation 24 hours a day to ensure efficient production
- Fast response to market demands: quick and flexible reactions to market requirements as well as unexpected situations
- Return on investment: the standard period is expected to be less than one year
ECO Solutions for blast furnace — Saving resources, creating value
Please follow the corresponding links to learn more about our competences.
Gas Cleaning
- MERIM – Maximized Emission Reduction and Energy Recovery
- WDS – Wet Dedusting System
- Casthouse and Stockhouse Dedusting
Energy Efficiency
By-Product Recycling
- Dry Slag Granulation with Heat Recovery
- Ferrous Briquetting – Recycling of by-products
- GasFerm – Generation of added value for offgases
ECO Consulting
TECHNOLOGY AND MODERNIZATION PACKAGES
Get striking results with incremental investments
Name | Short Description |
---|
Name | Short Description |
---|
Name | Short Description |
---|
Name | Short Description |
---|---|
Sequence Impulse Process (SIP) | Oxygen pulses for improved blast furnace gas utilization |
Scrap Profile Monitor | Fully automated 3D profile and volume measurement system for scrap piles |
Bag Break Monitor | Bag break detection and localization for pulse jet bag filter-plants |
Bend-resistant Copper Staves | Blast furnace cooling in high heat and liquid zones |
Wear-resistant Copper Staves | Wall cooling in higher heat zones of the blast furnace |
Material Type Monitor | Automatic identification of the type of material on conveyor belts |
Bag Cleaning Monitor | Acoustic monitoring of pulse jet bag filter plants |
Equipment Position Monitor | Reliable identification and tracking of metallurgical equipment throughout the steel plant |
Bag Filter Controller | Smart control of bag filter cleaning for dedusting plants |
Lance Checker | Test and diagnosis system for liquid iron and steel measuring devices |
VAiron BF optimizer | Process optimization for blast furnaces |
Lomas | Gas analysis system for very hot corrosive and dust-loaded process gases |
Name | Short Description |
---|
Name | Short Description |
---|