News & Press Releases
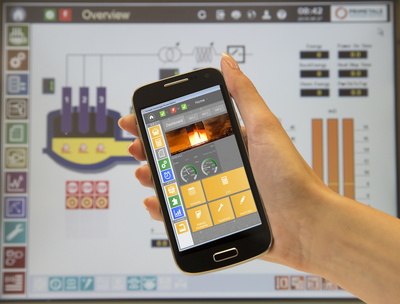
London, October 21, 2015
Primetals Technologies offers new electrode control system for electric arc and ladle furnaces
- Reduced energy consumption and increased melting efficiency due to auto-adaptive regulation algorithms
- Higher productivity ensured by automatic melting profiles and process parameter adaptation
- High reliability due to main focus on robustness and operational safety in an industrial environment
- Ensured process quality due to target group orientated screens and highly sophisticated data recording and evaluation
- Amortization within less than nine months
With „Melt Expert“, Primetals Technologies offers a new electrode control system for operators of electric arc and ladle furnaces. Melt Expert has been developed based on more than 35 years of experience with the Arcos and Simelt electrode control systems. The new system unifies the advantages of the previous solutions. New features like KPI (key performance indicator) indication, plant monitoring, customer orientated interfaces as well as sophisticated control strategies ensure most efficient production. Auto-adaptive regulation algorithms reduce energy consumption and increase melting efficiency. The system contains automatic melting profiles and adapts process parameters when required. This increases productivity. To ensure a high degree of reliability in a rough industrial environment, robustness and operational safety were a main focus during development. Amortization of Melt Expert may be achieved within less than nine months. For existing customers, Primetals Technologies offers upgrade kits to convert Arcos and Simelt systems to the new technology.
Melt Expert is based on an embedded controller platform, in which the system is split in a PLC part and a PC part. This new concept unifies the advantages of both platforms concerning flexibility, robustness and computing power, which is necessary for fast and complex calculations as well as high dynamic HMI. Control signal handling is done within the PLC part which simplifies the integration into the automation environment. Intelligent signal interface modules ensure very fast and accurate data sampling with on-board signal preconditioning.
Acquired data from hydraulics, mechanics and electrics is put in relation to actual operating conditions. In this way the electrode control system itself and its auxiliary systems are permanently monitored. So called health checks are performed automatically in regular intervals in which the functionality of measurement loops and output circuits are verified without disturbing the process. Continuous signal collection in combination with long-term-trend analysis allows the detection of shifts, deviations and creeping in malfunctions in a very early stage with the aim to predict a possible event or damage, before it happens.
Based on actual process conditions, control parameters such as set points or controller gains are automatically adapted by the system. Arc length will be modified according to process needs. This results in a higher melting efficiency and reduced energy consumption. A new algorithm is avoiding arc extinction and increase the power input during boring phase. An integrated loop gain linearization model transforms individual mechanical furnace characteristics and uniforms the control loops. Thus the parameter setup will be simplified which results in faster performance run ups and less time needed for optimization. Standard state of the art protection functions are included as well as more advanced modules like countermeasures against electrode oscillation.
Target group orientated screens provide conditioned information for different user needs like melt shop management, electrical / mechanical maintenance, operators, etc. Designated screens support optimization and parameter tuning for process experts. Regularly revisions are simplified by a special maintenance mode. A novel touch screen design allows simple and fast access to process relevant data and displaying key values such as actual consumption figures, melting time or regulation quality in the form of bench mark reports. Should there be a significant deviation from normal process parameters, related information comes alive and will be indicated. For fully automated process control additional packages like foaming slag control, melt down control and thermal furnace balancing are available.
SIMELT is a trademark of Siemens AG.
Primetals Technologies, Limited, headquartered in London, United Kingdom, is a pioneer and world leader in the fields of engineering, plant building, and the provision of lifecycle services for the metals industry. The company offers a complete technology, product, and services portfolio that includes integrated electrics and automation, digitalization, and environmental solutions. This covers every step of the iron and steel production chain—from the raw materials to the finished product—and includes the latest rolling solutions for the nonferrous metals sector. Primetals Technologies is a joint venture of Mitsubishi Heavy Industries and partners, with around 7,000 employees worldwide. To learn more about Primetals Technologies, visit the company website www.primetals.com.