News & Press Releases
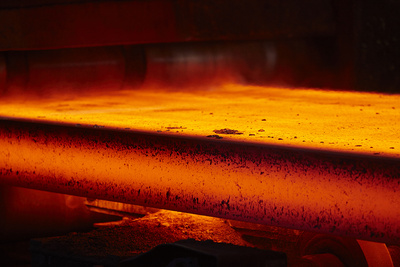
London, November 22, 2023
Primetals Technologies pioneers computer-vision-based artificial intelligence to reduce downtime at thyssenkrupp
- First-ever artificial intelligence solution for detecting strip cross cracks
- Improved detection of defects of the rolled intermediate products
- Reduces both operational downtime and risk of damage to mill equipment
- Provides mill operators with enhanced support functions
Primetals Technologies has implemented a digital assistant for detecting strip cross cracks at thyssenkrupp Hohenlimburg’s medium-wide hot-strip mill in Hagen, Germany. This digital assistant is Primetals Technologies first-ever computer-vision-based solution designed for its specific purpose.
Reduced downtime
The main benefits for thyssenkrupp are a reduction in downtime and wear related to the rolls of the hot strip mill. When a slab carries a cross-crack, it becomes visible in the roughing mill, and the size of the crack increases after each pass. When the transfer bars then enter the finishing mill, the crack may spread, further increase in size, and create holes in the rolled material. In the worst case, a defect like this can lead to cobbles in the finishing mill, with the risk of damaging the work rolls, backup rolls, and other production equipment.
To prevent transfer bars carrying strip cross cracks from entering the finishing mill, the cracks must be detected as early as possible in the process. In that way, operators can take action before a crack leads to equipment damage.
Instant alert
A camera located on the exit side of the roughing mill provides Primetals Technologies’ digital assistant with a live video stream. With the help of a machine learning model, which represents technology powered by artificial intelligence, the assistant processes the stream and checks for cracks. When the assistant detects a crack, it instantly alerts the operators. In addition, the information is transferred to the customer's intelligent business automation system for further analysis.
At thyssenkrupp Hohenlimburg, the digital assistant system will continuously optimize its performance, as it is self-learning and capable of identifying new types of cracks.
Modernization of drives
Headquartered in Hagen, Westphalia, thyssenkrupp Hohenlimburg employs a staff of around 900. The plant produces strip for the cold rolling industry as well as for direct processing, mainly for the automotive supply industry. Primetals Technologies has established a close partnership with the steel producer. An example of another current project is a research cooperation focused on fine-tuning process parameters using artificial intelligence algorithms. Among the recently completed projects is the modernization of the drive system of the plant’s hot-strip mill.
When cracks are detected early in the process, both unnecessary downtime and damage to equipment can be avoided.
The digital assistant uses AI to detect strip cross cracks and instantly alerts operators to such defects.
Primetals Technologies, Limited, headquartered in London, United Kingdom, is a pioneer and world leader in the fields of engineering, plant building, and the provision of lifecycle services for the metals industry. The company offers a complete technology, product, and services portfolio that includes integrated electrics and automation, digitalization, and environmental solutions. This covers every step of the iron and steel production chain—from the raw materials to the finished product—and includes the latest rolling solutions for the nonferrous metals sector. Primetals Technologies is a Group Company of Mitsubishi Heavy Industries, with around 7,000 employees worldwide. To learn more about Primetals Technologies, visit the company website www.primetals.com.