News & Press Releases
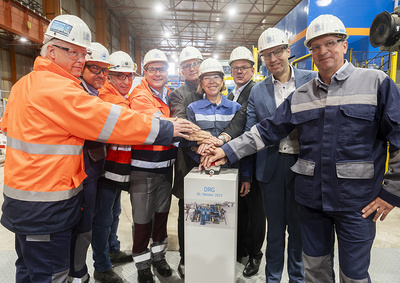
London, October 30, 2023
thyssenkrupp Steel’s new 2-stand reversing cold mill enables high-end production of silicon steel and AHSS
- Inauguration of Hyper UCM cold rolling mill, started up by thyssenkrupp Steel and Primetals Technologies
- thyssenkrupp Steel to manufacture harder and thinner flat steel products used in cars and motors for electrical vehicles
- World’s first 2-stand reversing cold mill featuring leading silicon steel technology Hyper UCM
- Boasts significantly higher production output compared to a single-stand mill
On September 26, German steel producer thyssenkrupp Steel produced the first coil on its new 2-stand reversing cold mill, supplied by Primetals Technologies. A centerpiece in the steel giant’s future plans, the mill was inaugurated on October 30 during a festive event at the Bochum, Germany, plant. During the inauguration, several specially invited guests gave speeches, including Heike Denecke-Arnold, Chief Operations Officer at thyssenkrupp Steel, and Thomas Eiskirch, mayor of Bochum.
“thyssenkrupp Steel wants to significantly strengthen its capabilities in high-strength steels and electromobility so we can differentiate ourselves even more consistently through the quality of our products,” said Heike Denecke-Arnold. “For example, with even thinner and stronger sheets, we want to further increase the energy efficiency and therefore the range of electric motors.”
The project posed some challenges to the Primetals Technologies team, as circumstances related to the pandemic and the war in Ukraine affected supply chains and delivery times. However, thanks to special efforts made in project management and effective and open communication, all scheduled milestones were met. Detailed 3D-models resulted in very smooth and effective pre-assembly works, and the whole mill, including its electrics and automation systems, was built in only six months.
Thinner and lighter
With its back-and-forth operation, the double reversing mill is capable of rolling particularly thin strip with an end-product thickness down to 0.2 millimeters, which is thinner than a fingernail. Featuring a highly versatile mill concept, the plant is, on the other hand, also capable of handling heavier gauges, i.e. products that meet the highest-possible strength requirements. Highly skilled operators supported by advanced automation solutions are the driving force behind achieving these extraordinary strip dimensions. “We are very excited to support thyssenkrupp Steel on its endeavor to further expand in the market for silicon steel,” said Hans-Jürgen Zeiher, Head of Electrics and Automation at Primetals Technologies. “The need for advanced high-strength steel grades used in electrical vehicles is projected to rise to extremely high levels over the coming decades. This mill ensures that thyssenkrupp Steel is well-prepared to deliver thinner and lighter steel of very high quality – exactly the type of steel needed in electrical vehicles.”
Market leader in cold rolling of silicon steel
A number of factors contributed to thyssenkrupp Steel’s decision to select Primetals Technologies as its supplier, one of them being strong references in Asia. The market leader in cold rolling solutions for the production of silicon steel, Primetals Technologies has a 90 percent market share in Asia. Another important factor is the unique features of the Hyper UCM technology. With this solution, it is possible for operators to influence the edges of the strip – the most common area for cracks – in a very flexible way.
A powerful payoff reel and a strip heating system in combination with Primetals Technologies’ Minimum Quantity Lubrication (MQL) system ensures smooth operation at the first rolling pass. The Hyper UCM is based on an optimized combination of roll diameters for work rolls and intermediate rolls. Thanks to this technology, mill operators can use work rolls of smaller diameters, a key success factor for achieving extremely light final gauges. Additionally, high-powered tension reels and various lubrication technologies reach higher reduction levels compared to conventional cold mills.
Optimizing the rolling process
Primetals Technologies supplied all mechanical equipment as well as electrics and automation for the mill, and is also responsible for installation and implementation. The automation solution also helps to enable the production of extremely thin and strong steel grades possible. For example, the Level 2 automation features compensation algorithms for coiler run out, roll eccentricity, and main drive utilization. In addition, proven process models for roll gap and roll and strip temperatures are implemented to support control over the whole rolling process as well as the settings related to flatness of the rolled material. A solution from Primetals Technologies for measuring flatness, the Contactless Shape Monitor, is integral to the advanced flatness control system.
Three large projects with thyssenkrupp Steel
In 2021, thyssenkrupp Steel placed a major order with Primetals Technologies for the reversing cold mill, a hot strip mill, and two continuous casters. All the projects are scheduled to be completed over the course of 2025. With an annual production volume of around 11 million tons of crude steel, thyssenkrupp Steel employs around 26,000 people across the world. thyssenkrupp Steel has set itself the goal of producing five million tons of CO2-neutral steel annually by 2030. By 2045 at the latest, the German steel producer wants its production to be climate neutral.
The inauguration ceremony took place on October 30. From left to right: Harald Espenhahn (Head of Technology and Environment Management, thyssenkrupp Steel), Ralf Häußler (Technology, thyssenkrupp Steel), Engin Karakurt (Works Council, thyssenkrupp Steel Bochum), Andy Rohe (Head of Downstream Operations, thyssenkrupp Steel), Thomas Wollinger (Managing Director, Bochum Economic Development), Heike Denecke-Arnold (Chief Operations Officer, thyssenkrupp Steel), Hans-Jürgen Zeiher (Executive Vice President, Primetals), Thomas Eiskirch (Lord Mayor of Bochum), and Markus Kovac (Plant Area Manager Bochum, thyssenkrupp Steel). Copyright: thyssenkrupp Steel.
Primetals Technologies, Limited, headquartered in London, United Kingdom, is a pioneer and world leader in the fields of engineering, plant building, and the provision of lifecycle services for the metals industry. The company offers a complete technology, product, and services portfolio that includes integrated electrics and automation, digitalization, and environmental solutions. This covers every step of the iron and steel production chain—from the raw materials to the finished product—and includes the latest rolling solutions for the nonferrous metals sector. Primetals Technologies is a Group Company of Mitsubishi Heavy Industries, with around 7,000 employees worldwide. To learn more about Primetals Technologies, visit the company website www.primetals.com.