HOT STRIP MILL — HIGHEST PERFORMANCE FOR NEW AND EXISTING STEEL MILLS
The demand for hot rolled strip is growing in multiple ways.
To remain competitive, new and existing mills must be as well prepared for this challenge as possible. The production of hot strip is a key element of steel production. Given that close to half of all steel produced is hot-rolled to strip, mills require maximum throughput and availability combined with geometrical precision and the ability to create optimum material properties.
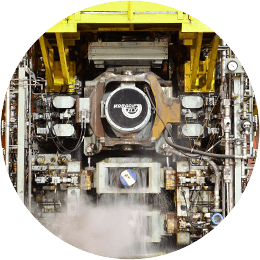
GLOBAL COMPETENCE IN HOT ROLLING
Primetals Technologies has extensive expertise in the design, manufacturing, installation and commissioning of Hot Strip Mills and equipment. Our comprehensive portfolio includes:
- Slab Sizing Press (SSP)
- Automatic Width Control (AWC)
- Heavy hydraulic edger for Roughing Mill
- Coil Box
- Encopanels® heat retention system
- Crop Shear
- Laminar cooling system
- PowerCooling®
- Pinch-roll quick exchange unit
- Eco Slide Disc
- Downcoiler
- Modular Coil Shuttle System (MCS)
- Sampling station
Additionally, our portfolio includes Finishing Mills with various advanced technologies for perfect strip:
- Pair Cross & SmartCrown® Technology for powerful profile and enhanced shape control
- Mill Stabilizing Device (MSD) for stable threading and rolling in demanding high reduction rolling
- Looper Shape Meter (LSM) for measuring shape of strip at interstand
- Work Roll Lubrication (WRL) for reduction in rolling force and for maintaining work roll surface quality
- Dynamic work roll cooling for control of work roll thermal crown
- Online Roll Profiler (ORP) for maintaining work roll surface quality by online grinding
Primetals Technologies offers two advanced solutions for trending endless rolling processing. One is Arvedi ESP, where the process produces hot strip in a combined, continuous, and uninterrupted casting and rolling process. The other is endless rolling for conventional hot strip rolling mills.
Want to know more? Go to Lifecycle Services & Integrated Plants & Solutions
COMPLETE AUTOMATION AND PROCESS CONTROL FOR HOT STRIP MILLS
Plant productivity and product quality are substantially depending on the quality of plant automation, process control, and available process optimization functions. Primetals Technologies provides standardized high-performance automation systems seamlessly integrating:
- Digitalization packages (e.g. TPO, MAT, Condition Monitoring, Intelligent Sensors)
- Production management systems (Level 3)
- Physical models combined with artificial intelligence (Level 2)
- Automation solutions including advanced technological controls (Level 1)
For existing installations, optimization packages are available as stand-alone solutions to improve production efficiency and strip quality.
Throughput maximization with:
- Mill Pacing including cooling beds charging optimization
- Strip Width Controller
Excellent strip quality with:
- Contour and Flatness Optimizer
- Comprehensive Temperature Model and Control (CTM and CTC)
- Strip Steering Control (SSE)
- Wedge and Camber Expert
- Microstructure Monitor (MSM)
Our solutions provide:
- Process Automation Twin to safely develop new materials and to optimize rolling schedules
- Central Operation Cockpit to support mill operation (centralized operation)
- Software architecture open for customers own future developments
- Modular structure for step-by-step modernizations
TECHNOLOGY AND MODERNIZATION PACKAGES
Get striking results with incremental investments
Name | Short Description |
---|---|
Contour and Flatness Optimizer | Measuring and optimization of strip contour and flatness |
Strip Width Controller | Control system for compensation of width deviations |
Microstructure Monitor | Determination of material properties for Hot Strip and Plate Mills |
Integrated Solenoid Valve (ISV) Spray System | ISV Roll coolant spray bars for hot and cold rolling mill strip flatness control |
Transformation Monitor | Measurement of % permeability of cooling steel on the ROT |
Strip Cooling Technology | Innovative and tailor-made strip cooling solution |
Modular Coil Shuttle System (MCS) | Rail-based, fully automated modular coil transport system |
Work Roll Lubrication | Work roll lubrication package for Hot Strip Mills and ESP plants |
ShapeMon HSM | Camber and centerline measurement for hot mills, plate mills, and ESP |
Encopanels | Heat retention system for Hot Strip Mills |
Wedge Camber Expert | Minimization of strip wedge and camber for Hot Mills |
Hot Mill Steering Expert | Strip steering and wedge control in HSM |
Roll Eccentricity Expert | Elimination of a known strip thickness quality disturbance from rolls |
TorqueMon | Inline measurement of roll spindle torque for rolling mills |
Position Transducer | Position measurement of rolling mill hydraulic capsule |
Width-Gauge Stereo Camera | Non-contact stereoscopic camera width-gauging systems for Hot Strip Mills |
Reference Story: The exhibition of state-of-art hot strip mill technology
Customer
Formosa Ha Tinh Steel Corporation, Ha Tinh, Vietnam
Type of plant
Hot strip mill
Our solution
An advanced Pair Cross mill with mill stabilizing device is used for stable operation of the process for producing thinner and harder steel. Meanwhile, a powerful crop shear and downcoiler are supplied to meet the increasingly complex requirements involved in the production of heavy gauge steel. For higher overall productivity, the slab sizing press is introduced for aggregation of slab width. Furthermore, to ensure smooth project execution, Primetals Technologies also provides first-class support for installation, erection, commisioning, and staff training.