STATE-OF-THE-ART SOLUTIONS FOR WIRE ROD AND BAR MILLS
Primetals Technologies has a complete portfolio of solutions for wire rod, bar, and non-ferrous mills. Deep knowledge that draws on more than 150 years of history from the tradition-rich brands of Morgan and Ashlow. Primetals Technologies has a record of more than 500 plants installed, and continues with ongoing innovation with hundreds of active industrial patents.
Today's demands for flexible and economic production of long products can only be met by production process, electrical and automation solutions that are based on precise process modeling, high-performance control systems and in-depth understanding of long product rolling technology. Drawing on more than a century of experience and proven solutions, Primetals Technologies has the answers to complex and diverse market demands – from the smallest upgrade to the greatest technical challenges for high-speed and special steel grade products. With our world-class equipment, processes and design tools, we set benchmarks for rolling long products. We offer worldwide proven and extensively preconfigured solutions, including modular standard packages as well as global and intelligent service concepts for the entire equipment lifecycle.
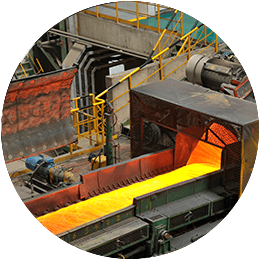
ROD MILL EQUIPMENT — THE MOST RELIABLE AND INNOVATIVE TECHNOLOGY FROM A SINGLE SOURCE
Speed, reliability and process flexibility are key to productive rod rolling operations - for high volume small sizes, maximum up-time, and multiple sizes/grades with quality tolerances, metallurgical and surface properties.
As long rolling’s technology pioneers, Primetals Technologies applies knowledge and experience to supply your ferrous and non-ferrous mill’s best solution. The leading provider of efficient wire rod mill technology with Morgan Vee No-Twist® Mills, Morgan Reducing/Sizing Mills, controlled cooling systems and thermomechanical rolling, we offer finishing blocks plus our High Speed Trim Shear and Morgan High Speed Laying Head to roll reliably at high speeds for superior coil packages. For more difficult steel grades, our versatile Morgan Stelmor conveyor system creates a wide range of cooling conditions. Our coil reforming, handling and compacting systems deliver the highest quality coil for demanding markets.
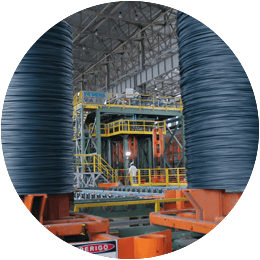
BAR MILL — SOLUTIONS TO ENSURE HIGH DURABILITY AND MAXIMUM AVAILABILITY
Systems and components are designed for high durability and maximum operation up-time, to meet the specific requirements of productivity, tolerance, surface finish and metallurgical quality.
Multi-slit and high-speed technologies ensure that the requirements of high productivity of rebars are safely and efficiently guaranteed. Through bar-in-coil operation, compact and twist free coils of bars and convex shapes are produced. State-of-the-art cooling technologies are available, for controlling the distortion of merchant bars, for thermo-mechanical rolling and for quenching & tempering both carbon and alloy grades, including stainless. Our reducing and sizing mill technology further improves the dimensional accuracy of bars with a better control of metallurgical structure.
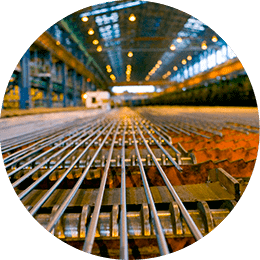
Endless Rolling
The cutting-edge technologies and processes for efficient rolling of bars and wirerod.
From our pioneering billet welding technology to Endless Bar Production (EBP), the processes and technologies for endless rolling of long products can play an important role in minimizing the consumption of energy, improving product consistency, and maximizing yield.
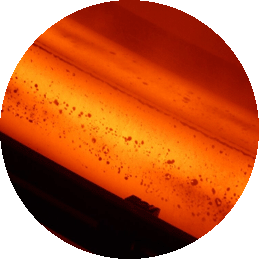