ALUMINUM FOIL MILL — EFFICIENT PRODUCTION OF HIGH-QUALITY, LOW-COST FOIL
The most advanced foil rolling mills in the world enable producers to achieve the highest quality foil at the lowest cost.
The increasing demand for ever higher quality and greater quantities of rolled aluminium foil has forced equipment manufacturers to adapt to new market requirements. 6 micron and below finished thicknesses are now the norm, along with rolling speeds of 2,000 m/min. Primetals Technologies has developed solutions that meet these demands; our mills are state-of-the-art, including features for high-speed operation and control, providing consistant production volumes. Our process know how and support ensures record start-up times with saleable coils produced from cold starts.
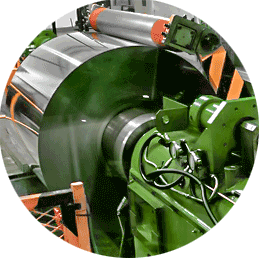
Aluminum Foil Mill — High quality, low cost production
Primetals Technologies' portfolio of Roughing, Intermediate, Finishing, Universal, and Bright Finish Foil mills is aligned with the market trend toward greater coil weights, combined with wider strip, thereby helping our customers to maximize yield and productivity. Offering a completely integrated automation and drive solution, including the latest generation of drive technology and a powerful automation platform, ensures:
- Rolling speeds of 2000 m/min
- Product widths of > 2000 mm
- Finished thickness of 0.0055 mm (5.5 microns)
Features:
- Air Bearing ShapeMeter (ABSM) roll provides highly sensitive solution for accurate flatness feedback
- Integral Solenoid Valve (ISV) sprays for improved flatness control
- Back-up roll chock cooling increases mill production through constant high-speed passes
- Edge trimming and scrap removal reduces the risk of strip breaks
- Vapor Shield fume cleaning and rolling oil recovery reduces harmful emissions
- Automated foil feed system for operator safety
- Fast work roll change sequence maximizes mill availability
- Mill bearing temperature monitoring, cooling & analysis is important with long high-speed passes
- Schneider Coolant Filtration maximises mill availability and minimizes waste
Want to know more? Go to Lifecycle Services & Integrated Plants & Solutions
Complete automation and process control for Aluminum Foil Mills
Plant productivity and product quality are governed to a large extent by the quality of plant automation, process control, and available process optimization functions.
- Digitalization packages (e.g. TPO, MAT, Condition Monitoring, Intelligent Sensors)
- Production management systems (Level 3)
- Physical models combined with artificial intelligence (Level 2)
- Automation solutions, including advanced technological controls (Level 1)
For existing installations, optimization packages are available as standalone solutions designed to improve production efficiency and strip quality.
Throughput maximization with:
- Production Optimization Modes
- Mill Set-Up System (MSU) as alternative to a model-based Level 2 system, including user-friendly pass schedule strorage and mathematical calculations
Excellent strip quality with:
- Automatic Gauge Control (AGC)
- Flatness Expert - Model-based Automatic Flatness control
Our solutions encompass:
- Central Operation Cockpit to support mill operation (centralized operation)
- Software architecture open for customers' own future developments
- Modular structure for step-by-step modernizations
TECHNOLOGY AND MODERNIZATION PACKAGES
Get striking results with incremental investments
Name | Short Description |
---|
Name | Short Description |
---|
Name | Short Description |
---|---|
TorqueMon | Inline measurement of roll spindle torque for rolling mills |
Modular Coil Shuttle System (MCS) | Rail-based, fully automated modular coil transport system |
Air Bearing Shapemeter | Shape measurement of rolled metal sheet and foil |
Schneider® Filter | Coolant Filtration System for rolling mills |
Hot Edge Sprays | Applying hot coolant to work rolls for tight edge correction |
Position Transducer | Position measurement of rolling mill hydraulic capsule |
Integrated Solenoid Valve (ISV) Spray System | ISV Roll coolant spray bars for hot and cold rolling mill strip flatness control |
Reference story: Top quality aluminium foil
Customer:
Jiangsu Dingsheng New Materials Joint-Stock Co., Ltd., China
Type of Plant:
Foil Mill
Our Solution:
Supply of 64 sets of Air Bearing ShapeMeters (ABSM) for reliable and accurate online shape measurement and Integral Solenoid Valve (ISV) spray systems, which effectively apply targeted zone cooling and lubrication, thereby reducing flatness errors, whilst controlling the bulk temperature of the mill.
What the customer says:
“We use Air Bearing Shapemeters and ISV spray bars from Primetals Technologies on most of our mills. We believe that its simple design ensures easy maintenance, low failure rate, high measurement accuracy, and high reliability, and fully meets the requirements of aluminum foil rolling mills.”
Dong Qingliang, Engineering Director Jiangsu Dingsheng New Materials