News & Press Releases
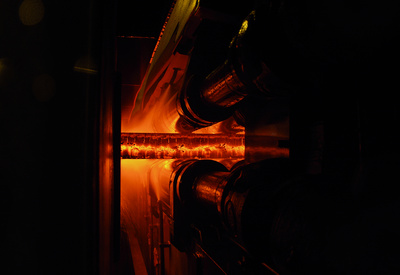
London, January 17, 2024
Primetals Technologies Advances Continuous Casting with Innovative Solution for Mold Level Control
- Utilizes advanced mathematical methods for next-level caster design optimization
- Reduces unsteady bulging by 50 percent
- Allows for higher casting speeds and greater productivity while producing slabs of reliable and high quality
For decades, Primetals Technologies has been refining the roll geometry of continuous casting machines, resulting in an increasingly stable mold level during the casting process. The most recent development is a ground-breaking model for establishing the ideal caster roll geometry already at the design stage.
Casting at higher speeds
This solution allows for a preview of how the caster will perform during operation, as it simulates both the unsteady bulging effect and mold level fluctuations caused by the phenomenon of bulging. The model enables steel producers to implement new or revamped casters that are designed to minimize mold level fluctuations during production. Therefore, they will be able to cast at higher speeds while producing slabs of high metallurgical quality.
A stable process during continuous casting is essential to produce high-quality products. Bulging is common and occurs as liquid steel at the core of the hot strand pushes against the shell of the slab as the strand moves between two rolls. During this process, heavy fluctuations in the mold level can build up, which might cause surface defects, or, in a worst-case scenario, a breakout, in which liquid steel pours out of the shell. Intensified bulging often results in operators having to reduce the casting speed.
Greater stability and product quality
Unsteady bulging is a complex problem involving, among other factors, mold level deviations, solidification in the mold, and shell growth in the secondary cooling zone. The newly developed model is designed to consider all these parameters. Utilizing Fourier transform, an advanced mathematical method, Primetals Technologies’ innovative software tool is capable of including a wide spectrum of parameters such as targeted steel grade, section size, and casting speed in its calculations. In this way, it identifies just the right frequency spectrum needed to set the optimal roll geometry.
Unsteady bulging reduced by 50 percent
Thanks to these simulations, it is possible to optimize the distance and diameter of the rolls before installing the equipment. Roll pitches are one of the main factors causing unsteady bulging, and by optimizing roll geometry, unsteady bulging is reduced by about 50 percent. Over the last months, this remarkable achievement was accomplished repeatedly at several steel plants where this solution is already implemented.
There are more benefits to be had with the new software model. Minimizing the occurrence of unstable bulging increases the caster’s range to include peritectic and ferritic steel grades, as no reduction in casting speed is necessary. Moreover, smoother strand shells and increased slab-surface quality are ensured.
The optimization of the rolls can be executed also for existing casters implemented by other plant builders.
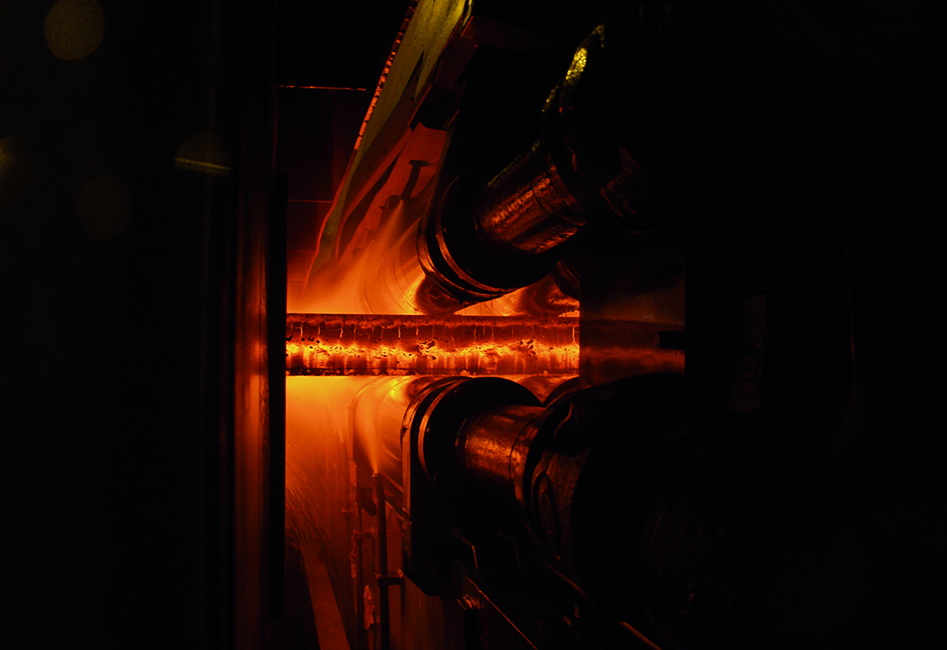
Primetals Technologies has developed a solution to optimize the continuous casting process by adjusting the distance and diameter of the rolls already before implementing the machine.
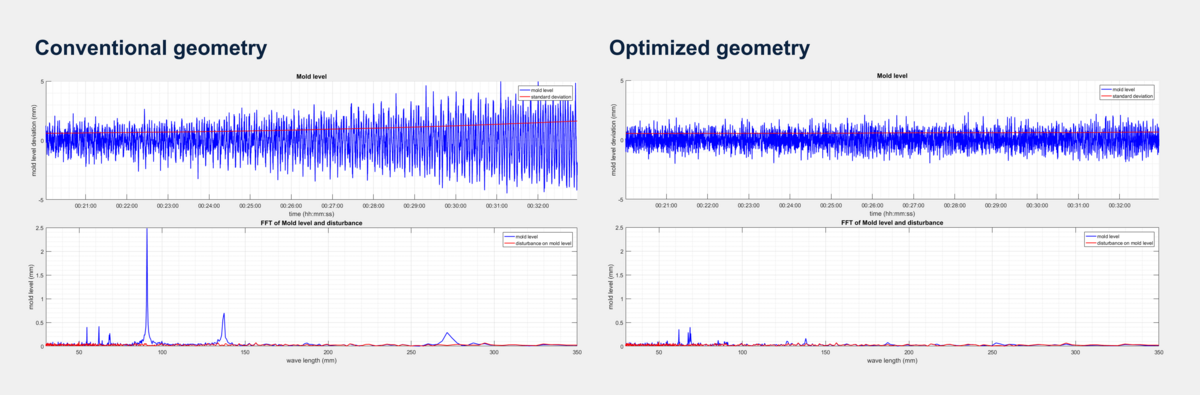
This graph visualizes the great discrepancy in stability between non-optimized and optimized casters, as it shows mold level deviation in a continuous caster before optimization (left side) and after optimization by Primetals Technologies (right side). The discrepancies are shown in the upper graph on both sides of the standard deviation curve indicated in red.
Primetals Technologies, Limited, headquartered in London, United Kingdom, is a pioneer and world leader in the fields of engineering, plant building, and the provision of lifecycle services for the metals industry. The company offers a complete technology, product, and services portfolio that includes integrated electrics and automation, digitalization, and environmental solutions. This covers every step of the iron and steel production chain—from the raw materials to the finished product—and includes the latest rolling solutions for the nonferrous metals sector. Primetals Technologies is a Group Company of Mitsubishi Heavy Industries, with around 7,000 employees worldwide. To learn more about Primetals Technologies, visit the company website www.primetals.com.