News & Press Releases
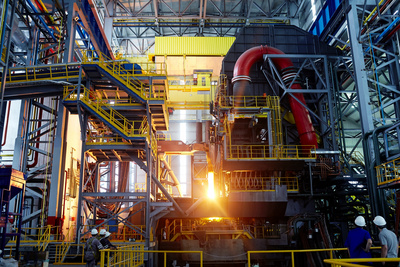
London, December 06, 2016
Primetals Technologies to supply new Minimill with EAF Quantum and WinLink to GPH Ispat in Bangladesh
Annual production capacity of 815,000 metric tons of long products and billets
World premiere: small investment equips plant with WinLink Flex to achieve virtually uninterrupted twin-roll casting at low running costs
EAF Quantum electric arc furnace and WinLink solution substantially reduce conversion costs
Products meet national and international standards
GPH Ispat set to become one of the country's leading steel producers
GPH Ispat Ltd., a manufacturer of long products based in Chittagong, Bangladesh, has commissioned Primetals Technologies to supply a minimill with a total annual capacity of 815,000 metric tons of finished products and billets. The order includes an EAF Quantum electric arc furnace, a ladle furnace, a three-strand, high-speed continuous billet caster, and a bar and section mill. WinLink Flex from Primetals Technologies will be installed for the first time worldwide. This concept not only allows virtually uninterrupted casting and rolling of long products, but also reduces investment and operating costs. The new minimill meltshop is scheduled to come into operation early 2018.
GPH Ispat is based in Chittagong in southeast Bangladesh. It produces rebars and profile steels, and has a current annual production capacity of 168,000 metric tons of billets and 150,000 metric tons of finished products. The new minimill will allow the company to substantially increase its capacities, and become one of the country's leading producers, serving the growing domestic and export markets.
Primetals Technologies will engineer and supply the processing equipment for the complete minimill meltshop. An EAF Quantum electric arc furnace with a tapping weight of 80 metric tons and a tap-to-tap time of 40 minutes will produce steel at a rate of up to 36 heats per day. The EAF Quantum cuts operating costs with energy consumption figures as low as 290 kilowatt hours per metric ton. A special automation solution will be implemented so that the electric arc furnace can be charged with various combinations of diverse mixtures of scrap metal, or with DRI and HBI. Further processing takes place in an 80-metric-ton ladle furnace with a heating rate of 4 °C per minute.
The three-strand continuous billet caster has a machine radius of ten meters, and casts around 815,000 metric tons per annum of billets with diameters ranging from 130 to 180 millimeters. The caster is directly connected to the downstream rolling mill. The high casting speed of up to six meters per minute and the compact size of the WinLink design allow two of the three strands to feed the downstream rolling line almost continuously. This eliminates the need for the usual reheating furnace; instead, an induction furnace heats the billets to the required temperature, again reducing investment and operating costs. The third strand produces billets for subsequent further processing or for sale on the market.
The bar and section mill has an annual production capacity of 640,000 metric tons at a maximum production rate of 120 metric tons per hour and a rolling speed of up to 27 meters per second.. The rolling line has 20 fifth-generation Red Ring stands, including horizontal, vertical, convertible and universal stands. If required, the line can be run in two-slit rolling mode. The scope of supply also includes a system for rapid stand change, water cooling, a system for transferring steel bars at speeds up to 27 meters per second to the cooling bed, which is 78 meters long and 11.2 meters wide, and a multi-strand stretch leveler. Primetals Technologies will also supply hot shears for cropping and dividing, a cold shear, a disk for cutting steel sections, a machine for counting rounds, mechanical and magnetic solutions for stacking and bundling finished products, and a banding station. In addition, there is secondary plant equipment, such as a mill workshop and laboratory, hydraulic and lubrication systems, special mechatronic packages, low-voltage supply, motors and drives, an uninterruptible power supply (UPS), as well as basic automation (Level 1) and process automation (Level 2). Primetals Technologies will also be responsible for supervising installation and commissioning work.
EAF Quantum electric arc furnace. A new Minimill with EAF Quantum and WinLink will be supplied to GPH Ispat in Bangladesh by Primetals Technologies.
Primetals Technologies, Limited headquartered in London, United Kingdom is a worldwide leading engineering, plant-building and lifecycle services partner for the metals industry. The company offers a complete technology, product and service portfolio that includes integrated electrics, automation and environmental solutions. This covers every step of the iron and steel production chain, extending from the raw materials to the finished product – in addition to the latest rolling solutions for the nonferrous metals sector. Primetals Technologies is a joint venture of Mitsubishi Heavy Industries (MHI) and Siemens. Mitsubishi-Hitachi Metals Machinery (MHMM) - an MHI consolidated group company with equity participation by Hitachi, Ltd. and the IHI Corporation - holds a 51% stake and Siemens a 49% stake in the joint venture. The company employs around 7,000 employees.