News & Press Releases
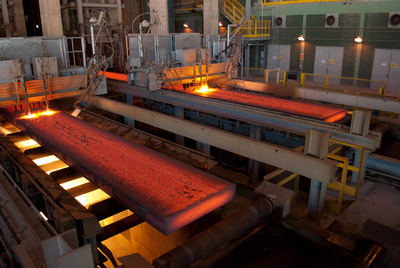
London, December 19, 2017
Primetals Technologies to supply two continuous slab casters and a hot rolling mill to the JSW Steel Dolvi plant
- Production capacity is 4.5 million metric tons of slabs per annum
- Technology packages ensure high slab quality
- JSW Steel already has two similar plants in operation in Toranagallu
- Casters will supply slabs to the new Primetals Technologies hot rolling mill
- Hot rolling mill has an annual capacity of 5 million metric tons per year
Primetals Technologies has won an order from JSW Steel Ltd., an Indian steel producer, to supply two continuous slab casters to its Dolvi plant in Maharashtra. Together, the two two-strand casters will have an initial annual capacity of around 4.5 million metric tons of slabs with future capacity potential for 6 million metric tons. The casters are scheduled to come on stream in the middle of 2019. A number of technology packages will ensure that the slabs have high internal and surface quality. The order to supply a hot rolling mill to the Dolvi site has also been received by Primetals Technologies. The hot rolling mill has an annual capacity of 5 million metric tons per year. JSW Steel already operates three continuous casting plants from Primetals Technologies at its steel works in Toranagallu, Karnataka.
JSW Steel is part of the JSW Group, and is one of India’s leading private steel producers. At its six locations in three Indian states, the company has a total installed production capacity of around 18 million metric tons of steel per annum. The steel works in Dolvi currently has an installed production capacity of around 5.0 million metric tons of steel per annum. The new casting plants and new hot rolling mill from Primetals Technologies, together with other capital investments, will substantially increase the location's capacity. In the medium term, JSW Steel has vision to increase its total production capacity to 40 million metric tons of steel per annum.
The two continuous casting plants from Primetals Technologies are designed as bow caster with straight SmartMold, and have a machine radius of nine meters and a metallurgical length of 34.5 meters, with a provision of 36.9 meters in future. Slabs will be cast with a thickness of 220 millimeters in widths ranging from 900 to 1,650 millimeters. The maximum casting speed will be just under two meters per minute with a provision of 2.1 meters per minute in future.
Primetals Technologies will install a number of technology packages to ensure not only a trouble-free casting process, but also slabs with high surface and internal quality. The packages include the Mold Expert breakout detection system, the LevCon mold level control, the DynaFlex mold oscillator, and the Quality Expert inline quality assurance system. Primetals Technologies will also supply the complete basic (level 1) and process automation (level 2) systems. DynaGap Soft Reduction in combination with Dynacs 3D cooling model will enable slabs to be cast from high-quality pipe grades and other micro-alloyed steels. Primetals Technologies will supervise installation and commissioning of the continuous casting plants, and train the customer's personnel.
The hot rolling line consists of one roughing stand with edger, a crop shear, a seven-stand finishing mill, three down coilers and a pallet conveyor. It produces hot strip with thicknesses from 1.5 to 16 millimeters and widths from 900 to 1,650 millimeters. The maximum coil weight is 34 metric tons. The mill can handle many different steel grades, including carbon structural steel, high quality carbon steel, low alloy
steel, DP & TRIP, as well as HSLA and API grades up to X-70. Primetals Technologies is responsible for the design, engineering and supply of the mechanical equipment. Four stands of the finishing mill are equipped with pair cross technology. Pair cross rolls consist of upper and lower work and backup rolls set at an angle to each other, so that each pair forms an X when viewed from above. This enables the roll gap to be set optimally for fine control of the profile of the rolling stock. Depending on the angle set, the crown of the strip can be varied within wider limits as would be possible with conventional four-high stands with work roll bending. Across the world, around 150 finishing stands are equipped with pair cross technology. Primetals Technologies will also supervise the erection and commissioning of the plant, and conduct the staff training. In addition, Primetals Technologies will supply the complete basic (level 1) and process (level 2) automation system, as well as all drives and motors for the rolling line.
Example of a continuous slab caster from Primetals Technologies. A similar caster will be installed in the Dolvi plant of JSW Steel in India.
Primetals Technologies, Limited, headquartered in London, United Kingdom, is a pioneer and world leader in the fields of engineering, plant building, and the provision of lifecycle services for the metals industry. The company offers a complete technology, product, and services portfolio that includes integrated electrics and automation, digitalization, and environmental solutions. This covers every step of the iron and steel production chain—from the raw materials to the finished product—and includes the latest rolling solutions for the nonferrous metals sector. Primetals Technologies is a joint venture of Mitsubishi Heavy Industries and partners, with around 7,000 employees worldwide. To learn more about Primetals Technologies, visit the company website www.primetals.com.