Optimizing coolant filtration to maximize yield, improve quality and achieve cost savings
With the market demanding increasingly high product quality it is essential that aluminium flat rollers have access to the latest tools and technologies to ensure operating costs remain under control, the environmental impact of operations are minimized without compromising product quality.
In this webinar we will look at the topic of coolant filtration and the detrimental impact poor filtration can have on the rolling process and finished product. From dirt and debris being rolled into the material causing surface quality issues like strip marking and pin holes, to coolant debris blocking spray nozzles and valves which are vital actuators for maintaining material flatness.
Solutions for achieving optimal coolant filtration and the benefits this delivers in terms of improving product quality, maximizing yield and optimizing operational processes to minimize costs will be presented.
Target audience:
- Mill Managers / Plant Managers / Operations Managers
- Maintenance Managers
- Technology Managers / R&D Managers
- Procurement Managers / Investment Managers
- Client Project Managers
Key takeaways:
- Understand the purpose and types of coolant for aluminum hot, cold and foil rolling mills
- Identify the causes of coolant contamination and the deterimetal impact this has on the rolling process and finished product quality
- Learn about the importance of coolant filtration and the world leading Schneider filtration system
- Discuss how the filter process can be optimized and the benefits that a fully optimized filter process can bring to an aluminum rolling mill
Speakers
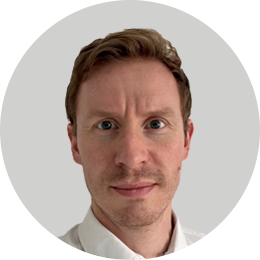
NICK SAUNDERS
Sales and Product Manager, Primetals Technologies, ShapeTech UK
Nick has worked exclusively in the metals industry since 2003, delivering major new plant and upgrade projects within the rolling and processing sector, with extensive experience specifically in aluminum. Nick’s roles have spanned many disciplines from fluids and mechanical engineering, project engineering, proposals and sales management.
Nick joined Primetals Technologies ShapeTech business in 2019 and is responsible for delivering sales of the ShapeTech product portfolio as well as sales of aluminum mill modernization and upgrade projects. Additionally, Nick is also the product manager for the Coolant Filtration system that will be featured and discussed in the webinar.
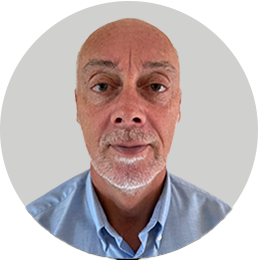
ANDY RICKETTS
Technical Sales, JR Schneider Co Inc, Benicia CA
In 2006 Andy Joined Primetals Technologies ShapeTech business. With 25 years experience in engineering design, management and manufacture, Andy was responsible for the Schneider filtration system. This role involved the design of coolant systems for both aluminium rolling mills and beverage can manufacture, using kerosene and water based coolants. Responsible for coolant filtration system design, from initial concept through to detail design and production documentation, involving specification then procurement of third party components and manufacture of filtration equipment. After joining J R Schneider in 2019, Andy travels worldwide providing consultancy services and process support, including coolant system and filter audits, leading to filtration quality optimization by on-site in-process iterative paper and media testing.
Moderator
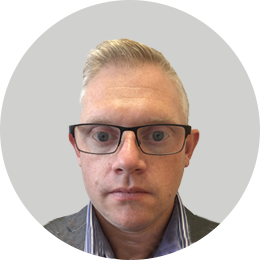
GRANT SHOEBRIDGE
General Manager, ShapeTech Primetals Technologies
With over 20 years experience working in various manufacturing sectors Grant joined Primetals Technologies in 2018. With a background in automation engineering Grant is dedicated to leading a business that delivers SMART solutions to solve the quality and production challenges of the metals industry.