BREAKTHROUGH BLAST FURNACE TECHNOLOGY WHICH REDUCES CO2 EMISSIONS AND DELIVERS A RAPID ROI
Reduced coke | Increased coal rate | Lower fuel rate | Minimized OPEX
Blast furnace operators face a huge challenge in responding to the ever-more stringent environmental targets and increasing adoption of carbon taxing. Sequence Impulse Process technology provides a significant step in supporting the transition to a carbon neutral steel production route.
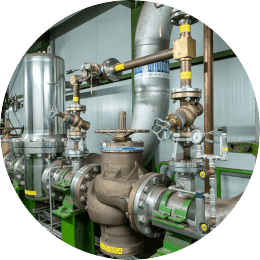
SIP - Delivers a unique combination of benefits
Invest in the future – benefit today
- Improved across furnace gas distribution and drainage, enhancing production potential
- Increased gas utilization, allows for an exchange of coke with higher rates of injected coal
- The net result is a reduction of total CO2 emissions
- Reduced total fuel rate results in lower OPEX
- Reduced CO2 emissions results in lower emission tax costs
- Offers a rapid Return on Investment (ROI) of typically 12 months
- Better furnace stability even with use of lower quality raw materials
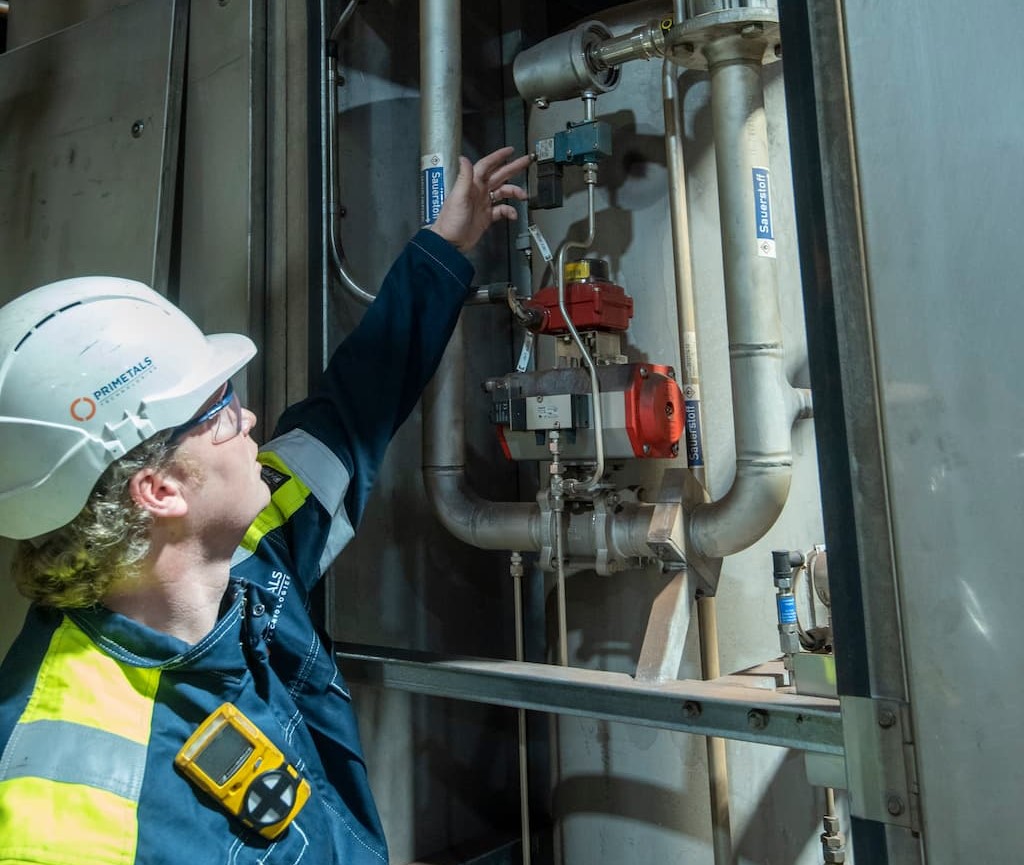
How does the Sequence Impulse Process work?
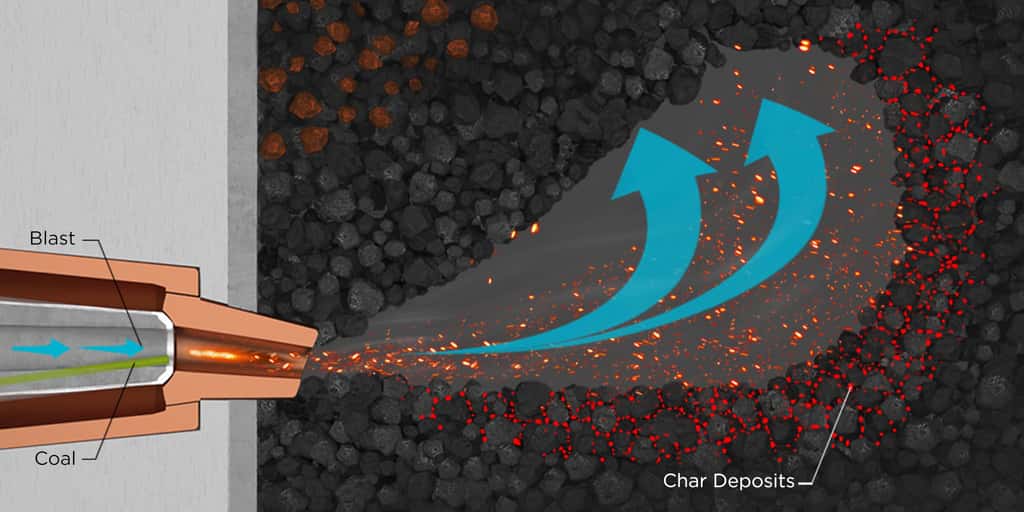
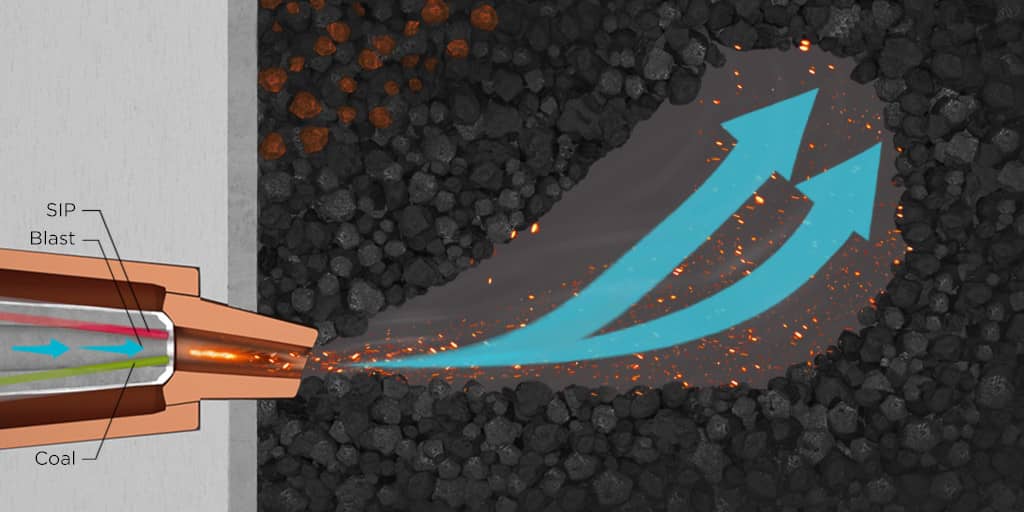
Improved combustion and conversion of fuel, leading to better gas distribution and drainage potential. Additionally, through higher penetration of the oxygen, the heat load generated is moved more to the central zone of the furnace.
- Coal injection into the blast furnace results in char materials accumulating, such that penetration of the ‘dead-man’ of coke is restricted.
- This limits the flow distribution into the center of the furnace and reduces gas utilization.
- By pulsing high-pressure oxygen in a pre-determined sequence to each tuyere, shock waves penetrate deep into the raceway of the blast furnace, combusting the fine char and improving coke permeability.
- This improves gas utilization and the potential for better furnace drainage.
Learn more about this ground breaking technology
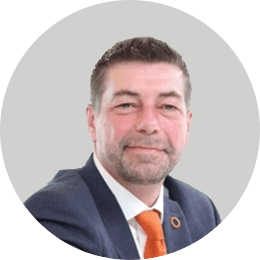
TALK TO OUR EXPERT
Colin Morrison
And hear about the operational results of SIP
A RAPID RETURN ON INVESTMENT FOR THYSSENKRUPP STEEL EUROPE
The first full-scale SIP system was installed at thyssenkrupp Steel Europe’s Duisburg plant on blast furnace ‘Schwelgern 1’ and began operation in Dec 2020. With a maximum annual capacity of 3.6 million tonnes of hot metal, Schwelgern 1 is one of the largest blast furnaces in Europe. The payback period on this project was under 12 months and the SIP technology has already reduced production costs by €8.5 per tonne of hot metal with potential for further improvement.
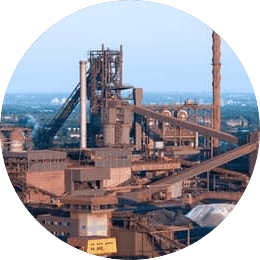
As a supporter and campaigner for the new technology in-house, I am of course very happy that it works reliably and safely. However, I would not have thought that even such 'small' amounts of SIP oxygen would have such a strong effect in the blast furnace. In this respect my respect my expectations have been exceeded.""
Manager Blast Furnace Technology
The task of every blast furnace operator is to produce pig iron at low costs with a high throughput. With the more stable furnace behavior and the cost savings on reducing agents, the SIP plant makes a significant contribution to this.""
Head of Blast Furnace Plant Schwelgern