Jump-Starting Decarbonization with Optimized processes and Increased Efficiency
Most plants in the metals value chain have enormous potential for emissions reduction without radical changes to production routes. Producers have to reach for these “low-hanging fruit” when taking their next steps toward zero-carbon 2050. Primetals Technologies offers a rich portfolio of technologies that help optimize processes, increase energy efficiency, and swiftly lower both costs and carbon emissions.
Crafted Scrap – Advanced Scrap Treatment
The growing commitment by the steel industry to reduce emissions and improve sustainability is leading to increasing interest in scrap-based steelmaking. The goal is to increase scrap utilization, either by installing new EAF capacity or by increasing the scrap ratio in BOF. Achieving this goal depends on the availability of high-grade scrap in which the chemical and physical characteristics have been controlled or on upgrading available qualities to satisfy the strict requirements of today’s steel.
The Advanced Scrap Management process combines artificial-vision and on-line analysis (LIBS or X-ray) with devices for scrap sorting and cleaning. This allows commercial scrap to be sorted into streams with specific quality ranges. The automatic and fully monitored operation of the scrap yard enables an accurate and efficient composition of the scrap load in the furnace, which results in higher performance and reduced emissions.
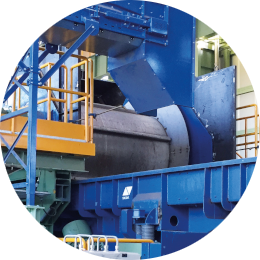
Scrap Rate Increase BOF
Steel is very easy to recycle with almost no quality loss and much lower emissions than in its original production route. Increasing the scrap rate in BOF converter steelmaking allows plant operators to reduce the amount of hot metal made in blast furnaces and as a result reduces CO2 emissions. Tools that improve the energy balance in converter operations and allow more scrap to be melted have already been developed, including process models and energy optimization, the dual-flow post-combustion lance, scrap preheating lances, and combined blowing converters.
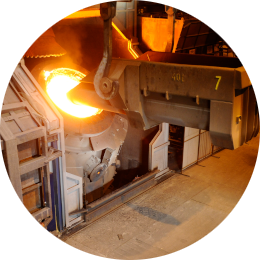
Smelter
The iron and steel industry is the second-largest industrial CO2 emitter. This is mainly caused by the high emissions generated during hot metal production in blast furnaces, which is still the dominant production route worldwide. Hydrogen-based direct reduction seems to be a promising alternative with much lower CO2 emissions. A two-step process is required to allow for direct reduction of low-grade ores, which are the majority of the ores available worldwide and the typical ore used in blast furnace. In the first step, the hot DRI is melted in the Smelter, a closed furnace with an electrode heating and reducing atmosphere. For final reduction of the DRI and to adjust the carbon content, coke is added to the Smelter along with the other charging materials. The hot metal produced in the furnace is then refined in the second step in a traditional BOF converter.
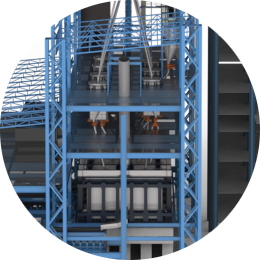
Premelt Process
The Premelt Process is a solution that allows existing converter plants to significantly reduce their overall CO2 output. Hot metal from the blast furnace is mixed with crude steel produced by the EAF and fed into the converter. This process is applicable in all BOF melt shops, and it’s especially attractive for converter shops with large heat sizes. Operators also benefit from an unchanged configuration in the BOF melt shop, significantly reduced cycle time, improved yield, lower investment costs from the outset, and help on their path to carbon-neutrality.
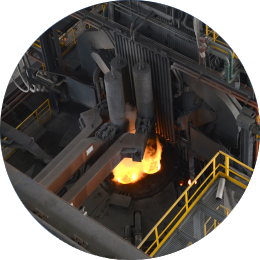
Arvedi ESP
The 180-meter-long Arvedi ESP (endless strip production) plant is far more compact than conventional casting and rolling mills and uses the heat of the cast strand for the first rolling step. An induction heater supports the second rolling step with minimum electrical energy and Arvedi ESP rolls with zero direct emissions. The Arvedi ESP line offers reproducible strip thicknesses down to 0.8 mm. This enables the production of high-quality, ultra-thin strips that can enter new market segments with direct application products and eliminates the cold rolling step. Hot rolling of direct application products optimizes not just the process itself but also the entire steel production route by eliminating unnecessary production steps, which reduces energy consumption and CO2 emissions.
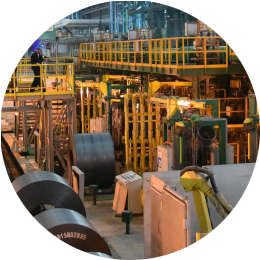
EAF Quantum®
The EAF Quantum is the most efficient electric arc furnace in the world. It’s designed to handle scrap steel of varying composition and quality. The EAF Quantum combines proven elements of shaft furnace technology with an innovative scrap charging process, an efficient preheating system, a new tilting concept for the lower shell, and an optimized tapping system. This all adds up to very short melting cycles and a reduction of CO2 emissions by up to 30 percent per ton of crude steel.
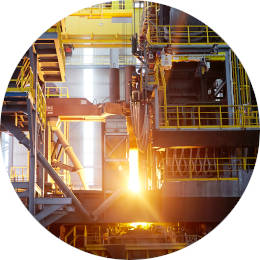
EAF Fusion
The EAF Fusion is designed to replace BOFs in integrated steel plants. With a tap weight up to 250 tons, it can handle raw materials like hot metal, scrap, HBI, DRI, and pig iron in many different combinations. The EAF Fusion offers a smooth transition from high hot metal ratios to pure scrap-based operation. The fully automated furnace enables a safe and highly efficient melting process and is equipped with the most modern connective features to make the furnace ready for Industry 4.0 applications. EAF Fusion is a highly flexible electric arc furnace that will help plant operators meet future carbon reduction goals.
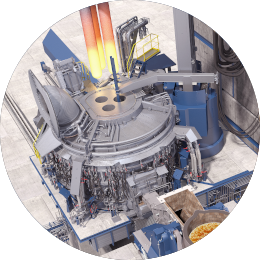
Sequence Impulse Process
Sequence Impulse Process (known as SIP for short) offers blast furnace operators the opportunity to reduce their CO2 emissions, lower operating costs and improve productivity. The innovative technology works by injecting high energy pulses of oxygen into the raceway of the furnace via a lance. The pulse clears char material that builds-up in the ‘dead-man’. This enables greater gas distribution and utilization and improves the overall furnace drainage. With a quick return on investment, SIP technology offers operators an immediate solution to reduce CO2 emissions and improve the green credentials of their plant.

HOT BLAST STOVES
Optimized hot blast stove technology provides a major opportunity to reduce the blast furnace fuel rate and to reduce the enrichment gas requirement for stoves’ gas combustion. These both lead directly to reduced CO2 emissions. The top fired stove technology offered by Primetals Technologies allows hot blast temperatures above 1300°C and requires a relatively low dome temperature compared to other technologies. A side-benefit of this is a reduction of thermal NOx generation.
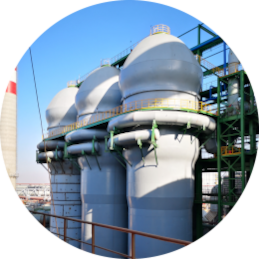
ENERGY-SAVING STAVES
Energy loss to the blast furnace cooling system has a direct impact on the fuel rate and therefore the CO2 emissions from a blast furnace. Primetals Technologies has developed solutions for staves which help to insulate the stave from the process heat, providing up to 5kg/tHM fuel saving. The solutions also ensure that during periods of furnace instability, the heat losses to the cooling system are significantly reduced. The patented solutions also reduce the risk of stave erosion by providing a “stone-box” effect. Energy saving staves were first installed in August 2019 and are currently installed on three blast furnaces.
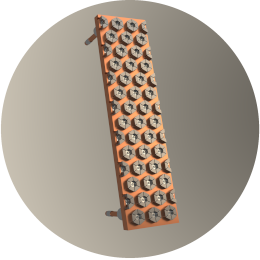