PELLETIZING TECHNOLOGY — PLANTS, REVAMPS, MODERNIZATIONS, AUDITS, STUDIES, AND TEST WORKS
Primetals Technologies offers the full range of pelletizing capacities, from the smaller capacities involving unique Circular Pelletizing Technology (0.5 - 2.0 mtpa) to larger capacities based on straight travelling grate technology (from 1.5 up to 9 mtpa).
To be able to meet customers’ diverse pelletizing requirements, Primetals Technologies developed a comprehensive package of tools based on extensive industry expertise that allows the full spectrum of operational challenges to be met quickly and efficiently – customized to individual needs. The cornerstone of Primetals Technologies' pelletizing solutions is a combination of in-depth practical investigation (on-site plant audits, pot grate test work) and theoretical analyses (plant simulations, process calculations). This enables Primetals Technologies to develop technical concepts for new pelletizing plants, as well as for revamps or performance upgrades of existing plants. Thanks to Primetals Technologies’ solutions, pelletizing plants can be improved with selective measures and debottlenecking initiatives can be implemented, for example through burner management, grain size control, process automation, and emission reduction.
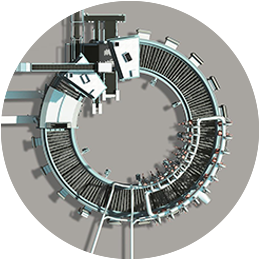
KNOW-HOW AND TECHNOLOGIES FOR PELLETIZING
Straight grate pelletizing plant
Covering a range of 1.5 to 9.0 million tons of pellets per year, our straight grate pelletizing plants provide an efficient way to produce any kind of pellets with the greatest operational flexibility.
Circular Pelletizing Plant
The building footprint of the induration furnace is significantly smaller compared with the straight grate process, which means that the world’s most compact pelletizing plant – with its low building profile, short process air ducts, and standardized equipment - allows the cost of iron production to be slashed.
Revamp of pelletizing plants
With customers eager to take their pelletizing plant operations to the next level, Primetals Technologies is able to offer highly effective and cost-efficient revamping solutions based on vast operational knowledge, in-depth process and plant analysis, and the experience gained from numerous refurbishment projects.
Modernization packages
Even small-scale modernization packages can have a major impact on overall plant performance and the operational expenditures of a pelletizing plant. These types of solution can be implemented in a relatively short space of time, resulting in an impressive and quick return on investment.
Typical examples of these modernization packages include:
- High-efficiency burner meeting the highest environmental standards and capable of reducing fuel consumption
- Green pellet online size control for more uniform pellets, which increases the efficiency of the process gas flow during induration
- Pallet car widening by up to 10% for increased production
- Diagnostic pallet car delivering process data directly from the pellet bed during operation for analysis and improvement of process parameters
Pellet pot grate test works
Primetals Technologies’ most modern in-house pot test facility enables our specialists to analyze raw materials of all types, evaluate the optimum raw mix for pellets, and develop optimized process parameters for the induration process.
Pelletizing plant configuration/simulation model
Primetals Technologies has developed a superior process simulation model for the indurating process that takes account of specific plant configurations as well as any physical parameters, chemical reactions, and thermodynamic processes that influence the indurating process. This allows our specialists to determine the optimum plant design for both new and existing plants.
Plant optimization audits and studies
External plant assessment and analysis are often the first steps involved in developing a project or setting improvement targets for a customer. Primetals Technologies has experienced engineers in all disciplines who have the skills and experience to carry out plant optimization audits and studies.
Want to know more? Go to Lifecycle Services & Integrated Plants & Solutions.
Intelligent process optimization for pelletizing plants
The ultimate aim in pelletizing is to produce consistently high pellet quality while ensuring high productivity rates and low conversion costs, while at the same time meeting strict emission targets. Owing to the mutual interdependence of the different pelletizing process steps, precise simulation is essential to reliable process optimization.
Continuous and seamless operation across working shifts is key to maintaining stable process conditions and maximum output. A reliable process control system based on objective assessment of all relevant production conditions helps the operator to make informed operational decisions for setpoints and process parameters. This ensures maximum production of quality pellets at minimum production costs.
Our solution
Primetals Technologies has developed an Expert System for pelletizing plants based on advanced process models that provide additional insight into the process and facilitate operational decisions. The pellets in the different layers of the pellet bed - on the outside or in the center face - are subject to different process conditions, so the process models predict, evaluate, and track these conditions on a fine-meshed grid in all cross-sections throughout the whole induration process. Extended simulation capabilities support the identification of optimal operational points in order, for example, to optimize the trade-off between the energy supply to the different process steps in the drying, firing, and cooling zones.
Advantages
- High productivity and reduced energy consumption; the pelletizing plant runs at peak performance while minimizing consumption of fuel gas and electrical energy for process fans
- Best product quality; the chemical and physical properties of the pellet product are maintained at the desired levels
- Stable and shift-independent operation; best-practice pelletizing plant operation 24 hours a day to ensure efficient production
- Return on investment; the standard period is expected to be less than one year
ECO SOLUTIONS FOR PELLETIZING PLANTS — SAVING RESOURCES, CREATING VALUE
Please follow the corresponding links to learn more about our competences.
Gas Cleaning
- Room dedusting
- MEROS – Maximized emission reduction of pelletizing plants, especially DeSOx
- SCR DeNOx-plants for reducing NOx
ECO Consulting
Energy Efficiency
TECHNOLOGY AND MODERNIZATION PACKAGES
Get striking results with incremental investments
Name | Short Description |
---|---|
Scrap Profile Monitor | Fully automated 3D profile and volume measurement system for scrap piles |
Discharge Monitor | Acoustic monitoring of truck or wagon discharging |
VAiron Pelletizing Optimizer | Process optimization for pelletizing plants |
Equipment Position Monitor | Reliable identification and tracking of metallurgical equipment throughout the steel plant |
Name | Short Description |
---|
Name | Short Description |
---|
Name | Short Description |
---|
Name | Short Description |
---|
Name | Short Description |
---|
Reference Story: The world’s first Circular Pelletizing Plant designed by Primetals Technologies
Customer
Pro Minerals Pvt. Ltd., India
Type of plant
Circular Pelletizing Plant (191 m²), output 1.0 mtpy
Our solution
Our solution for the production of merchant pellets was devised as a green-field installation of a Circular Pelletizing Plant (CPT), including several associated facilities such as units for grinding and filtration and a beneficiation plant for upgradation of low-grade iron ores. Primetals Technologies was chosen to design the core pelletizing plant, which encompasses mixing, green pelletizing, and product classification, as well as the circular induration furnace, an in-house development of Primetals Technologies.
The basis for the design was the production of pellets suitable for coal-based direct-reduction production at a capacity of 1.0 million tons per year.
The CPT concept is based on the smart combination of the well-proven travelling-grate process with the simple, compact, and robust mechanical design of a circular dip-rail cooler. This results in a pelletizing plant with a small footprint and low space requirements. Moreover, the CPT plant ensures the highly efficient use of equipment, low operational expenses, and fully automated process control and operation, all of which means there are several advantages over conventional pelletizing plants.
In October 2020 the CPT was started up successfully, resulting in the world’s first production of pellets using this new technology.