News & Press Releases
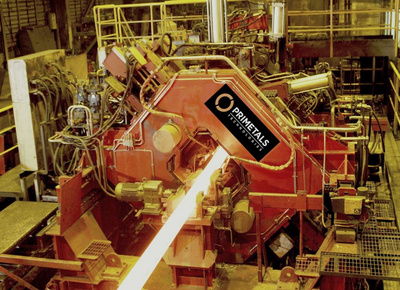
London, November 30, 2017
Primetals Technologies supplies ERT-EBROS billet welding system for rolling mill of Ferriera Valsabbia
- Welded billets permit endless rolling with high product quality
- Considerable boost in plant output and utilization levels
- First use of ERT-EBROS in Italy
Italian steel producer Ferriera Valsabbia S.p.A. has placed an order with Primetals Technologies to supply ERT-EBROS endless rolling technology for the company's existing bar rolling mill in Odolo, Brescia province. The aim is to boost plant output and utilization levels. The system welds together billets intended for rolling, thus enabling a continuous rolling process with a consistently high product quality. The new ERT-EBROS plant is scheduled to commence operation in September 2018. It is the first ERT-EBROS system in Italy.
Primetals Technologies is responsible for the project engineering as well as for assembly and commissioning supervision of the new equipment, and will be supplying the ERT-EBROS billet welding system, including a deburring station, extraction system and complementary equipment such as pinch roll, shear and roller table. The ERT-EBROS system will be designed for an annual production capacity of 900,000 metric tons. The scope of supply also includes the fluid systems, the electrical equipment and automation system and also technology packages for controlling the welding. An induction furnace installed before the rolling train will make up for temperature losses.
Established in 1954, privately owned Ferriera Valsabbia operates an EAF-based minimill with a production capacity of some 900,000 metric tons per year of billets and bars for concrete reinforcement (rebars). It is among the largest rebar producers in Italy. The bar rolling mill was realized by Primetals Technologies in 2007/2008. This included the installation of a hot-charging system for billets as well as a system for single-bar high-speed delivery that allows rolling speeds of up to 29 meters per second in two-slit rolling mode. The mill is designed to process low-carbon steel billets with a square cross-section of 150 x 150 (160 x 160 in the future) millimeters and length of 9 meters. This results in rebars with diameters of between 8 and 40 millimeters. In two-slit rolling mode, the bar diameters from 8 to 20 millimeters can be realized.
The ERT-EBROS system welds consecutive billets together so that, once joined in this way, they can be processed in an endless rolling process. This increases output, cutting the time otherwise taken by two billets between rolling. Utilization of cooling bed capacity can be enhanced and production of customized coil weights is also possible. ERT-EBROS is installed between the reheating furnace and the first roll stand and uses a flash welding process with fast and intensive heating. This results in solid-state joining of the billets without the need for additional filler metal. A dynamic flash control system helps to control all the process parameters in real time and thus ensures high joint quality as well as reduced energy consumption and material loss.
After welding and head upsetting, joints are deburred on a self-cleaning deburring station. The deburring machine operates independently of the welding unit and so the cycle time is not increased. Active spatter protection protects the mechanical and electrical equipment from steel spatters. This is crucial for process quality, extends components' useful lives and facilitates maintenance. The core of the electrical system is the integrated high-frequency transformers. These compact components are extremely reliable and can perform an indefinite number of welding operations without maintenance. Each transformer is equipped with diodes that convert the high-frequency square-wave voltage into a stable, extremely flat DC voltage. The square-wave voltage is generated by converters with which the current can be controlled ten times faster than with thyristor circuits. A stable voltage and short control times are essential for a stable and repeatable process flow.
EBROS is a registered trademark of Steel Plantech Co.
ERT-EBROS is a registered trademark of Primetals Technologies in some countries
ERT-EBROS billet welding system from Primetals Technologies. A similar system will be installed at Ferriera Valsabbia S.p.A. in Odolo, Italy.
Primetals Technologies, Limited, headquartered in London, United Kingdom, is a pioneer and world leader in the fields of engineering, plant building, and the provision of lifecycle services for the metals industry. The company offers a complete technology, product, and services portfolio that includes integrated electrics and automation, digitalization, and environmental solutions. This covers every step of the iron and steel production chain—from the raw materials to the finished product—and includes the latest rolling solutions for the nonferrous metals sector. Primetals Technologies is a joint venture of Mitsubishi Heavy Industries and partners, with around 7,000 employees worldwide. To learn more about Primetals Technologies, visit the company website www.primetals.com.