News & Press Releases
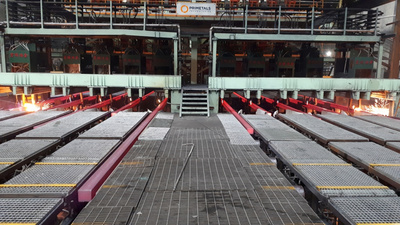
London, February 23, 2021
Zenith Steel starts-up billet caster with SRD segments and technological packages from Primetals Technologies
- World's first application of SRD (Single-Roll DynaGap) segments in billet caster
- SRD segments enable final solidification point to be followed precisely
- Soft and Hard Reduction to be applied by SRD segments
- Individually controlled rolls adjust optimally to strand condition
- Technological packages further enhance internal billet quality
In January, a 10-strand billet caster upgraded by Primetals Technologies was started up in the converter steel making plant #3 in Changzhou of Chinese steel producer Zenith Steel Group Co., Ltd. (Zenith Steel). The billet caster is the first one worldwide to be equipped with the new SRD (Single-Roll DynaGap) segments. The SRD segment has been specially developed for use in the area of final solidification, and it enables the upper rolls to be pressed down individually onto the solidifying strand. This enables the final solidification point to be followed precisely. Technological packages like DynaPhase, Dynacs 3D and DynaGap SoftReduction 3D further improve the internal billet quality with regard to center porosity and center segregation.
The 10-strand billet caster of Zenith Steel in its Changzhou, Jiangsu Province plant has a rated capacity of 2 million metric tons per year. It produces section with a cross section of 160 x 160 millimeters at a maximum casting speed of 2.4 meters per minute. Steel grades processed include low, medium and high carbon steels as well as tube, spring, cold heading and tyre cord steels.
Precise knowledge of the final solidification point and the associated soft reduction is needed to reliably produce billets for steel grades that require high internal quality. The new SRD segments from Primetals Technologies can be applied to the final solidification precisely. This enables each individual roll gap to be adjusted dynamically as a function of the steel grade, overheating, cooling or casting speed. Each roll transmits an individual force, which makes even higher thickness reduction rates possible, and reduces the segregation and porosity in the center of the strand. Additionally, thickness reduction of the billet or bloom also after final solidification is possible. This process is defined as Hard Reduction and can furthermore reduce the porosity of the cast billet and bloom.
SRD segments are designed for long operating cycles and easy maintenance. For example, each roll has its own overload protection, which prevents damage to the bearings and surfaces of the rolls. The rolls are embedded in a function unit so that they can be quickly replaced in a maintenance workshop. The individual roll units can also be tested and calibrated before installation of the segments in the caster.
Technological packages supplied by Primetals Technologies include process models for soft and hard reduction, namely DynaPhase, Dynacs 3D and DynaGap SoftReduction 3D. The DynaPhase online thermodynamic phase transformation model calculates material properties like thermal enthalpy, thermal conductivity, density and solid fraction. The Dynacs 3D secondary-cooling model is capable of calculating the full 3D strand-temperature profile at any position along the strand for optimum adjustment of the secondary-cooling setpoints and the determination of the point of final strand solidification. Finally, DynaGap SoftReduction 3D fully automatic roll-gap control system allows for dynamic soft reduction to minimize centerline segregation for improved internal strand quality
Within the modernization project, Primetals Technologies was also responsible for the basic and detail engineering and supply of mechanical equipment like roller blocks, spray header and WSU units as well as the complete basic (level 1) automation system and process optimization application (level 2).
Zenith Steel is privately owned and operates an integrated steel mill in Changzhou in the Jiangsu province of China. The company's steel mill has a production capacity of more than ten million metric tons of steel per year. Zenith Steel manufactures a wide range of end products, including steel pipes, bearing and spring steel, and various structural steels. In 2011, Primetals Technologies supplied a bloom caster for big round casting sections, and in 2016 added a casting section format of 280x320 mm.
10-strand billet caster at the Changzhou converter steelmaking plant #3 of Chinese steel producer Zenith Steel. The caster was supplied by Primetals Technologies and is equipped with SRD segments for hard reduction and special technological packages.
Primetals Technologies, Limited, headquartered in London, United Kingdom, is a pioneer and world leader in the fields of engineering, plant building, and the provision of lifecycle services for the metals industry. The company offers a complete technology, product, and services portfolio that includes integrated electrics and automation, digitalization, and environmental solutions. This covers every step of the iron and steel production chain—from the raw materials to the finished product—and includes the latest rolling solutions for the nonferrous metals sector. Primetals Technologies is a joint venture of Mitsubishi Heavy Industries and partners, with around 7,000 employees worldwide. To learn more about Primetals Technologies, visit the company website www.primetals.com.