News & Press Releases
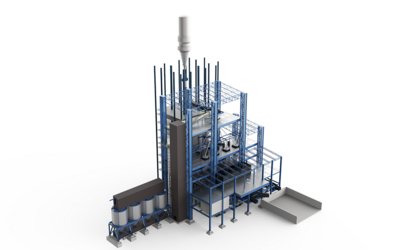
London, November 02, 2022
Primetals Technologies and RHI Magnesita develop new melting technology for low grade DRI
- Designed to replace the blast furnace
- Reduces CO2 emissions to a minimum
- Technology ready for implementation
Most of the CO2 emissions in steelmaking comes from the blast furnace process, which today is still the main production route. Primetals Technologies is developing a new green steel technology to replace blast furnace plants and has signed a collaboration contract with RHI Magnesita, the global leader in refractory innovations.
Greatly reduced CO2 emissions
The new solution is called the Smelter, a furnace powered by electrical energy and used for melting and final reduction of direct reduced iron (DRI). Operated together with a direct reduction plant and an LD converter (BOF), the Smelter is producing hot metal for the steelmaking plant and liquid slag that can be used in the cement industry.
The conventional BF – LD converter route results in almost two tons of CO2 per ton of liquid steel. Thanks to the new technology, CO2 emissions will be reduced by a factor of six, to 0.33 tons of CO2 per ton of liquid steel.
"If you are serious about green steel, you have to start with the blast furnace processes, i.e. where the CO2 emissions are massive. RHI Magnesita has been working closely with both steel and non-ferrous industries around the world for years. We are proud to be an integral part of the push for the development of green steel production solutions together with Primetals Technologies, not only as supplier of refractories but also as a technology partner,” says Constantin Beelitz, President Europe, CIS & Turkey at RHI Magnesita.
Gerald Wimmer, Vice President of Converter Steelmaking, Primetals Technologies, adds: “RHI Magnesita and Primetals Technologies have extensive experience in the development of new technologies. That is an excellent base for successfully developing just the right technology for steel producers who struggle to find a replacement for the blast furnace.”
Plant transitionwithout downtime
For steel producers, there are two main cost related benefits that comes with the Smelter. The DR – Smelter – LD converter route can be used especially for low grade iron ores, as it handles the generated slag well. Additionally, the LD converter is kept when the Smelter is implemented. Therefore, steel producers who operate integrated plants do not need to modify the rest of their production chain and do not have to renew their certifications when they invest in a Smelter.
It will also be possible to keep the blast furnace running while installing the Smelter, and to then discontinue the use of the old equipment as soon as the Smelter is ready for operation.
Ensuring a long lifetime
An important part of the Smelter, the refractory material protects the furnace shell by containing hot metal at temperatures of at least 1,500° Celsius. Consisting of bricks, it expands when heated and endures extremely high temperatures. The performance of the refractory material is determined by several factors, such as size, quality, mechanical furnace design, and cooling solutions. RHI Magnesita and Primetals Technologies have put their heads together and found a reliable refractory solution for the Smelter, which will ensure high productivity and a long lifetime.
Ready for the market
In the coming years, more and more steel producers will invest in green steel technology. The Smelter is a sensible and still environmentally friendly option to extend the lifetime of existing integrated steel plants, as there will be just minor adjustments necessary at the plant.
Primetals Technologies’ and RHI Magnesitas’ collaboration has already been in effect for some time and several simulations were executed in the project over the last months. Therefore, the Smelter is ready for the market.
A 3D rendered image of the Smelter from Primetals Technologies.
Primetals Technologies, Limited, headquartered in London, United Kingdom, is a pioneer and world leader in the fields of engineering, plant building, and the provision of lifecycle services for the metals industry. The company offers a complete technology, product, and services portfolio that includes integrated electrics and automation, digitalization, and environmental solutions. This covers every step of the iron and steel production chain—from the raw materials to the finished product—and includes the latest rolling solutions for the nonferrous metals sector. Primetals Technologies is a joint venture of Mitsubishi Heavy Industries and partners, with around 7,000 employees worldwide. To learn more about Primetals Technologies, visit the company website www.primetals.com.