News & Press Releases
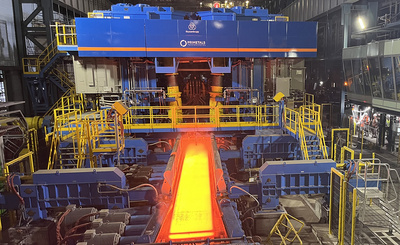
London, July 04, 2025
thyssenkrupp Steel and Primetals Technologies Start Up Slab Caster and Hot-Strip Mill in Duisburg
- Enable thyssenkrupp Steel to produce high-strength steel grades and adapt to current and future market demands
- Advanced continuous slab caster with state-of-the-art process optimization systems ensures highly efficient casting
- Primetals Technologies awarded comprehensive service contract for slab caster
- Modernized hot-strip mill equipped with advanced automation solution for high quality, increased productivity, and stable operations
On July 4, 2025, thyssenkrupp Steel and Primetals Technologies have celebrated the successful startup of slab caster No. 4 and hot-strip mill No. 4, both supplied by Primetals Technologies, at thyssenkrupp’s Bruckhausen site in Duisburg, Germany. The ceremony was attended by political and industry leaders, including Mona Neubaur, Minister of Economic Affairs and Climate Protection, as well as top executives from both companies.
Flexible and Future-Proof Production
The project separated the former combined casting and rolling line into two distinct units: a revamped caster and a modernized hot-strip mill. As a result, thyssenkrupp Steel increased capacity from 1.8 to 3.1 million tons per year and aligned its product range with future markets and a focus on profitable premium products.
"This project is a decisive milestone in strengthening our leadership in technological and quality terms, while meeting the increasing expectations of our customers,” said Dennis Grimm, CEO of thyssenkrupp Steel. “We now possess one of the most modern production networks in the European steel industry. This will enable us to optimize our slab and hot-strip qualities significantly with the aim of further developing our product portfolio in line with future requirements, particularly in the case of multi-phase steels, high-strength steels, and grades for electric mobility and the energy turnaround.”
The project faced several challenges, including a tight schedule and up to 1,000 workers on-site simultaneously. Thanks to close collaboration and strong project management, Primetals Technologies completed the project on time. As an example, the roughing mill and descaler were preassembled next to the existing line, allowing for rapid installation during the scheduled shutdown.
“Over the past several months of construction work and commissioning, Primetals Technologies and thyssenkrupp Steel have worked closely together to reach this significant milestone. Our teams have definitely gone the extra mile—both on the construction site and throughout the planning and engineering phases—to ensure the success of this challenging project, all while operating under intense time constraints,” said Hans-Juergen Zeiher, Executive Vice President and Head of Global Business Unit Electrics and Automation at Primetals Technologies. “I want to extend my heartfelt gratitude to all Primetals Technologies employees involved in the project for their outstanding dedication. I would also like to thank thyssenkrupp Steel and our partners for their expertise and support. This successful startup would not have been possible without our strong collaboration.”
State-of-the-Art Slab Caster
The upgraded 2-strand continuous caster No. 4 processes slabs from 900 to 1,800 millimeters wide and 257 millimeters thick. It includes advanced mechanical and automation solutions. The DynaWidth mold-width adjustment system enables fast and flexible slab-width changes, while the DynaFlex hydraulic oscillator improves strand-surface quality by adjusting mold-oscillation parameters. The Level 2 automation system, CC Optimizer, features modules like Dynacs 3D, which ensures optimal secondary cooling.
New Caster Maintenance Contract
The partnership between thyssenkrupp Steel and Primetals Technologies has also led to a two-year maintenance contract for the ECO-star roller repair and services on caster No. 4. This agreement aims to stabilize production, extend roller lifetime, and ensure reliable operation. With the support of the Maintenance and Asset Technology (MAT) platform, a computerized maintenance management system, Primetals Technologies will provide comprehensive roller maintenance, including inspection, refurbishment, and technical support, to maintain optimal caster performance and high-quality output.
Modern Hot-Strip Mill with Intelligent Control Systems
The hot-strip mill includes a single-stand 4-high reversing roughing mill with attached edger and patented Encopanels. The first two finishing mill stands and the strip cooling system have been upgraded, along with a comprehensive Level 1 and 2 automation system.
The modernized hot-strip mill allows thyssenkrupp Steel to improve yield and expand its product portfolio, including high-strength steel and grades for the e-mobility sector. This is made possible by the Encopanels, which retain heat in the transfer bar, increased rolling and bending force at the finishing mill, and the precise Level 1 and Level 2 automation system.
The mill enhancements are managed by advanced automation solutions, such as the Contour and Flatness Optimizer. Together, these systems ensure precise control of the strip rolling process, while maintaining high quality, productivity, and stable operations, even when process requirements change, such as product dimensions or steel grades. The extended laminar cooling section, equipped with precise Level 2 strip cooling models, allows for accurate cooling profiles and temperature control, enabling consistent material properties.
Major Modernization Order
The project is part of a broader modernization plan. In 2021, thyssenkrupp Steel ordered a reversing cold mill, the hot-strip mill, and two thick-slab continuous casters from Primetals Technologies. The cold mill produced its first coil in September 2023 at the Bochum site, and slab caster No. 3 is scheduled for 2026.
With an annual production volume of about 11 million tons of crude steel, thyssenkrupp Steel employs around 26,000 people worldwide. The company aims to produce five million tons of CO₂-neutral steel per year by 2030 and achieve full climate neutrality in production by 2045.
Representatives from thyssenkrupp Steel and Primetals Technologies commemorate the successful startup of slab caster No. 4 and hot-strip mill No. 4, both supplied by Primetals Technologies. Photo copyright: thyssenkrupp Steel.
The modernized hot-strip mill from Primetals Technologies allows thyssenkrupp Steel to improve yield and expand its product portfolio.
thyssenkrupp Steel’s new continuous caster No. 4 from Primetals Technologies features advanced mechanical and automation solutions.
A ceremony held at thyssenkrupp Steel’s Bruckhausen site in Duisburg commemorated the startup of slab caster No. 4 and hot-strip mill No. 4 supplied by Primetals Technologies. From left to right: Dr. Harald Espenhahn, Head of Technology, Environment & Maintenance, Dennis Grimm, CEO of thyssenkrupp Steel, Mona Neubaur, Minister of Economic Affairs and Climate Protection, Ilse Henne, Chairwoman of the Supervisory Board, thyssenkrupp Steel, Sören Link, Lord Mayor of Duisburg. Photo copyright: thyssenkrupp Steel.
Primetals Technologies, Limited, headquartered in London, United Kingdom, is a pioneer and world leader in the fields of engineering, plant building, and the provision of lifecycle services for the metals industry. The company offers a complete technology, product, and services portfolio that includes integrated electrics and automation, digitalization, and environmental solutions. This covers every step of the iron and steel production chain—from the raw materials to the finished product—and includes the latest rolling solutions for the nonferrous metals sector. Primetals Technologies is a Group Company of Mitsubishi Heavy Industries, with around 7,000 employees worldwide. To learn more about Primetals Technologies, visit the company website www.primetals.com.